What is Rogers 4835 PCB?
RO4835 laminates are a low loss material that offer low cost circuit fabrication, compatible with standard epoxy/glass (FR-4) processes. These laminates are available with Rogers proprietary LoPro® Reverse treated copper foil, ideal for applications requiring low insertion loss.
Features
- RoHS compliant for applications requiring UL 94 V-0
- IPC-4103 compliant
- Dielectric constant (Dk) of 3.48 +/- .05
- Dissipation factor of 0.0037 at 10 GHz
Benefits
- Ten times improved oxidation resistance, compared to traditional thermoset laminates
- Superior high frequency application compatibility due to excellent electrical performance
- No blistering or delamination
- Reliable Plated through Hole (PTH) construction
Rogers 4835 PCB Manufacturer.Rogers 4835 PCBs are manufactured by industry-leading experts, ensuring precision and reliability in high-frequency applications.
Rogers 4835 PCB is a high-performance printed circuit board (PCB) widely used in the electronics field. What makes it special is the use of high-quality materials – Rogers Corporation’s 4835 material. This material is designed to meet the stringent requirements of high-frequency and high-speed applications, including wireless communications, radio frequency circuits and microwave technology. Rogers 4835 PCB is highly regarded for its excellent electrical performance, thermal performance, and dimensional stability.
Rogers 4835 sheet has a number of key properties that make it ideal for high frequency applications. First, it has extremely low dielectric loss, which means that almost no energy is lost during signal transmission, thus maintaining signal clarity and accuracy. Secondly, a stable dielectric constant ensures signal consistency at different frequencies, which is particularly important for RF and microwave circuit design. In addition, the excellent dimensional stability of Rogers 4835 PCB means that its physical dimensions change minimally under different temperature and humidity conditions, helping to maintain circuit stability and reliability.
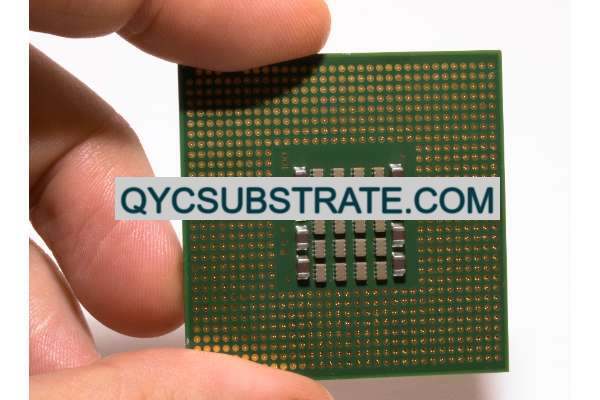
Rogers 4835 PCB Manufacturer
Rogers 4835 PCB exhibits excellent performance and suitability in many areas. In terms of communication technology, especially the rapid development of 5G communication, the demand for high-frequency circuits is increasing day by day. Rogers 4835 PCB supports high-speed data transmission and precision signal processing, providing a reliable foundation for modern communications equipment. In addition, this advanced PCB technology is widely used in RF front-end equipment, radar systems, and RF applications in medical equipment.
Designing a Rogers 4835 PCB requires a combination of material properties and circuit layout effects. Engineers often use advanced computer-aided design (CAD) software to precisely plan circuit layouts to minimize signal transmission paths and reduce potential electromagnetic interference. The manufacturing process includes multiple process steps such as lamination, electroless copper plating, drilling and metallization to ensure that the quality and stability of each PCB meets design requirements.
Rogers 4835 PCB has become one of the first choices for high-frequency and high-speed electronic equipment due to its excellent electrical characteristics, thermal performance and dimensional stability. Whether in the construction of communication infrastructure, the application of satellite communications or high-frequency technology in the medical field, this PCB technology can provide reliable support for various complex electronic systems. Its excellent performance makes it widely recognized in the industry and continues to promote the development and innovation of electronic technology.
The types of Rogers 4835 PCB
When it comes to high frequency and high speed applications, Rogers 4835 PCB offers a variety of design options to suit different circuit layouts and application needs. The following is a detailed introduction to the different types of Rogers 4835 PCB:
Rogers 4835 PCB is mainly divided into single-layer, double-layer and multi-layer boards, each type has its own unique advantages and applicability in design and application.
Single-layer PCB is the simplest and basic type of circuit board, suitable for relatively simple circuit designs and low-cost applications. It consists of a base material (such as Rogers 4835 material), a conductive copper layer, and a surface protection layer. Single-layer PCBs are cheaper to manufacture because they have only one layer of conductive copper and the circuit layout is relatively simple, making them suitable for preliminary prototype development or the production of simple electronic devices. In certain low-complexity applications, such as some consumer electronics or electronic toys, single-layer PCBs are an affordable option.
A double-layer PCB consists of two layers of conductive copper, one on the top and one on the bottom, separated by an insulating layer (such as Rogers 4835 board). This structure allows for more complex circuit layouts and a higher level of integration because it provides more ways to connect circuits. Double-layer PCBs are widely used in communications infrastructure, industrial control systems, and medical equipment to support application requirements that require more complex signal processing and data transmission. For example, medical equipment often requires the integration of multiple sensors and control units, and double-layer PCBs can effectively support the implementation of these functions.
Multilayer PCBs have three or more conductive copper layers that are laminated together using multilayer stacking technology and an insulating layer (usually Rogers 4835 material). The main advantages of multilayer PCBs are their higher circuit density and more complex design capabilities. They can support more device integration, more complex signal transmission paths and higher frequency requirements. Multilayer PCBs are commonly used in satellite communications, high-speed data transmission systems, and advanced medical imaging equipment because they provide highly stable signal transmission and circuit performance.
In summary, the different types of Rogers 4835 PCBs (single-layer, dual-layer, and multi-layer) each have unique characteristics and suitability to meet the design requirements of a wide range of electronic devices and applications, from simple to complex. Choosing the appropriate PCB type depends on the specific application scenario, circuit complexity and performance requirements.
The advantages of Rogers 4835 PCB
The Rogers 4835 PCB is a high-performance printed circuit board (PCB) using special materials developed by Rogers Corporation. It exhibits excellent properties in high-frequency and high-speed applications in electronic equipment, providing significant advantages over traditional FR-4 sheets.
The material of Rogers 4835 PCB has a stable dielectric constant and low dielectric loss, making it particularly suitable for applications requiring high-frequency signal transmission. In wireless communications, radar systems, and radio frequency circuits, high-frequency characteristics determine the stability and accuracy of signal transmission. Rogers 4835 PCB maintains high signal fidelity and effectively reduces signal attenuation and distortion, thereby improving overall system performance and reliability.
Rogers 4835 PCB exhibits lower dielectric losses compared to traditional FR-4 boards. In high-speed data transmission and precision signal processing, loss reduction means less energy loss and clearer signal output. This is critical for applications that require a high degree of accuracy and stability, such as satellite communications, data center networks and high-speed computer servers.
Rogers 4835 material has excellent thermal conductivity and thermal stability to effectively manage heat in circuits. In environments with high power density and long operating times, the stability and reliability of a circuit board are directly dependent on its thermal management capabilities. Rogers 4835 PCB can quickly conduct and dissipate heat in the circuit to avoid overheating, thereby extending the life of the device and improving performance.
The materials of Rogers 4835 PCB have undergone rigorous engineering verification and long-term experiments to ensure its stability and reliability under various environmental conditions. Advanced technology and strict quality control measures are used in the manufacturing process to ensure the manufacturing accuracy and consistency of each PCB. This makes Rogers 4835 PCB one of the first choices for many electronic equipment manufacturers and system integrators.
Due to its excellent performance characteristics, Rogers 4835 PCB is widely used in communication facilities, satellite communications, aerospace technology, medical equipment, and industrial automation. These applications have extremely high requirements for high-frequency characteristics, low loss and stability of circuit boards. Rogers 4835 PCB can meet and exceed these requirements, providing customers with reliable solutions and excellent performance.
To sum up, Rogers 4835 PCB is favored in the electronics industry for its excellent high-frequency characteristics, low loss and stable thermal performance. It not only improves the performance level of electronic equipment, but also brings significant contributions to technological innovation and product reliability.
How to Design a Rogers 4835 PCB?
The Rogers 4835 PCB is a high-performance printed circuit board (PCB) using special materials developed by Rogers Corporation. It exhibits excellent properties in high-frequency and high-speed applications in electronic equipment, providing significant advantages over traditional FR-4 sheets.
The material of Rogers 4835 PCB has a stable dielectric constant and low dielectric loss, making it particularly suitable for applications requiring high-frequency signal transmission. In wireless communications, radar systems, and radio frequency circuits, high-frequency characteristics determine the stability and accuracy of signal transmission. Rogers 4835 PCB maintains high signal fidelity and effectively reduces signal attenuation and distortion, thereby improving overall system performance and reliability.
Rogers 4835 PCB exhibits lower dielectric losses compared to traditional FR-4 boards. In high-speed data transmission and precision signal processing, loss reduction means less energy loss and clearer signal output. This is critical for applications that require a high degree of accuracy and stability, such as satellite communications, data center networks and high-speed computer servers.
Rogers 4835 material has excellent thermal conductivity and thermal stability to effectively manage heat in circuits. In environments with high power density and long operating times, the stability and reliability of a circuit board are directly dependent on its thermal management capabilities. Rogers 4835 PCB can quickly conduct and dissipate heat in the circuit to avoid overheating, thereby extending the life of the device and improving performance.
The materials of Rogers 4835 PCB have undergone rigorous engineering verification and long-term experiments to ensure its stability and reliability under various environmental conditions. Advanced technology and strict quality control measures are used in the manufacturing process to ensure the manufacturing accuracy and consistency of each PCB. This makes Rogers 4835 PCB one of the first choices for many electronic equipment manufacturers and system integrators.
Due to its excellent performance characteristics, Rogers 4835 PCB is widely used in communication facilities, satellite communications, aerospace technology, medical equipment, and industrial automation. These applications have extremely high requirements for high-frequency characteristics, low loss and stability of circuit boards. Rogers 4835 PCB can meet and exceed these requirements, providing customers with reliable solutions and excellent performance.
To sum up, Rogers 4835 PCB is favored in the electronics industry for its excellent high-frequency characteristics, low loss and stable thermal performance. It not only improves the performance level of electronic equipment, but also brings significant contributions to technological innovation and product reliability.
Why use ceramic Rogers 4835 PCB over other boards?
In modern electronics design, selecting the right PCB material for a specific application is critical. Rogers 4835 PCB is an excellent high-frequency material, but compared to traditional fiberglass reinforced boards (FR-4 boards), ceramic PCBs (such as alumina ceramics) show clear advantages in some specific application scenarios. Here are a few of the main reasons why ceramic PCBs are chosen for high-temperature environments and high-frequency signal transmission:
Ceramic PCB materials typically have higher thermal conductivities than common resin-based materials such as FR-4, which means they can disperse and manage heat in circuits more efficiently. In devices with high power densities and long operating times, heat buildup can lead to performance degradation or even device damage. The excellent thermal conductivity of ceramic PCBs helps maintain a stable operating temperature of the board, extending the life of the device.
Ceramic PCBs maintain their mechanical stability in high-temperature and high-humidity environments and are not prone to changes in size or performance due to environmental changes. This property is particularly important in applications that require long-term reliability and durability, such as aerospace, automotive electronics, and medical equipment.
Ceramic PCBs typically have a low dielectric constant, which means it reduces signal loss and distortion during transmission. Especially in the RF and microwave bands, accurate signal transmission is critical to system performance. Ceramic PCB can provide a clearer and more stable signal transmission path, ensuring high performance and reliability of the device.
Ceramic PCB materials generally have good chemical stability and are resistant to chemicals and liquids. This makes it more suitable for applications in some special environments, such as industrial control systems or military equipment, where corrosive substances are often exposed.
Due to their excellent electrical properties and durability, ceramic PCBs excel in demanding applications. They maintain stable electrical performance under extreme conditions, such as high temperature, humidity or vibration, while still delivering consistent performance.
In summary, ceramic PCBs are chosen primarily for their ability to provide superior performance and reliability over conventional PCBs in high frequencies, high temperatures, and demanding environments. These characteristics make ceramic PCBs the first choice for many high-end electronic devices and systems, with important application value and development potential in both commercial and industrial applications.
What is the Rogers 4835 PCB Fabrication Process?
Manufacturing the Rogers 4835 PCB is a complex and precise process involving multiple steps to ensure the final product meets demanding electrical and mechanical performance standards. Below are the detailed process steps for manufacturing Rogers 4835 PCB and their importance:
First, the manufacturing process begins with the material selection and pre-processing stages. Rogers 4835 board material selection is critical as it determines the overall performance of the PCB. These materials require strict quality control and pre-treatment before production to ensure that their surfaces are smooth and defect-free and clean and dust-free to avoid problems in subsequent process steps.
Next comes the lamination process, which is one of the crucial steps in PCB manufacturing. During the lamination process, selected panels of Rogers 4835 are stacked together according to design requirements, often with a specific adhesive applied between each layer. After the stacking is completed, the entire stack of panels is placed in a high-temperature and high-pressure environment, and the adhesive between the layers is cured through thermal pressure to form a strong overall structure.
Subsequent process steps include drilling, electroless copper plating and patterning. The drilling process is used to create holes in the PCB for subsequent component mounting and circuit connections. Electroless copper plating is used to form conductive paths on and within the PCB to provide a good electrical connection. Patterning is the transfer of designed circuit patterns to the PCB surface, usually through photolithography and etching, to ensure the accuracy and precision of conductive paths.
Finally, metallization and surface treatment are used to enhance the connection reliability and durability of the PCB. The metallization process involves plating gold or tin on the PCB surface and inside the holes to protect the wires and provide a good soldering surface. Surface preparation typically involves covering the PCB with a protective layer that protects the PCB from chemical corrosion or mechanical damage in the environment.
Throughout the manufacturing process, it is crucial to strictly control each process parameter and quality inspection. This includes verification of the original properties of the material, temperature and pressure control of the lamination process, monitoring of drilling accuracy, uniformity inspection of electroless copper plating, and electrical testing of the final PCB. Only in this way can you ensure that each Rogers 4835 PCB has consistent performance and reliability that meets the stringent requirements of the purpose for which it was designed.
In short, the manufacturing of Rogers 4835 PCB not only requires advanced technology and equipment support, but also requires highly professional process control and quality management to ensure its excellent performance and long-term stability in high-frequency and high-speed applications.
The application of ceramic Rogers 4835 PCB
Rogers 4835 PCB is a printed circuit board designed for high-frequency and high-speed electronic applications, using Rogers Corporation’s 4835 material with excellent electrical and thermal properties. Due to its excellent performance, Rogers 4835 PCB is widely used in several key industries. The following are its main application areas and features:
Rogers 4835 PCBs play a key role in modern communications infrastructure, such as mobile communications networks and base station equipment. These devices need to handle large amounts of data transmission and frequent signal exchange, requiring circuit boards with highly stable signal transmission capabilities and good anti-interference properties. Rogers 4835 PCB’s low dielectric loss and stable dielectric constant ensure high signal fidelity and stability, supporting reliable device operation.
Satellite communication systems place extremely high requirements on the reliability and performance of electronic equipment, especially in space environments. Rogers 4835 PCB is the first choice due to its excellent thermal stability and high temperature resistance, which can maintain stable operation under extreme temperature changes and space radiation conditions. It supports complex signal processing and data transmission tasks in satellite receiving and transmitting equipment, ensuring efficient transmission and processing of information.
Radar systems require high-precision signal processing and fast response capabilities to detect and track targets. The high frequency characteristics and excellent signal integrity of Rogers 4835 PCB make it widely used in radar antenna control units and signal processing modules. Its stable performance ensures reliable operation of radar systems in various complex environmental conditions, including maritime, air and land applications.
In the medical industry, electronic equipment is required to efficiently process and transmit physiological signals and medical data while ensuring the safety and stability of the equipment. Rogers 4835 PCBs play an important role in medical diagnostic equipment, monitoring instruments, and medical imaging systems. Its high-speed data transmission capabilities and excellent signal fidelity ensure accurate collection and transmission of medical data, supporting medical staff to make timely and accurate diagnoses.
The aerospace field has extremely stringent requirements for electronic equipment, which must be able to operate reliably at high altitudes and in extreme environments. The high temperature stability and mechanical strength of Rogers 4835 PCB make it ideal for critical electronic systems in satellites, aircraft and spacecraft. It is capable of withstanding highly dynamic loads and vibrations while maintaining circuit integrity and performance stability.
In short, Rogers 4835 PCB has demonstrated excellent application value and technology in many fields such as communications, satellites, radar, medical and aerospace with its excellent high-frequency characteristics, stable signal transmission capabilities and reliable thermal management performance Advantage. Whether it supports data processing, sensor control or communication connections, it has made important contributions to the design and performance improvement of modern electronic devices.
FAQs
What frequency range applications is Rogers 4835 PCB suitable for?
The Rogers 4835 PCB is primarily designed for use in a wide range of high frequency applications, typically covering frequency ranges from a few hundred megahertz to several gigahertz. This makes it very suitable for 5G communications, radio frequency front-end equipment, microwave communication systems and other application scenarios that require high-frequency transmission and precise signal processing. The superior electrical characteristics and stability of the Rogers 4835 PCB ensure excellent performance in these high-speed data transmission environments.
How is the thermal management of the Rogers 4835 PCB?
Rogers 4835 PCB material has excellent thermal conductivity and thermal stability to effectively manage heat in circuits. This makes it particularly suitable for applications requiring high power density and long operation times. In high-frequency and high-speed circuits, heat buildup can have a negative impact on signal stability and circuit life. Therefore, the good thermal management capabilities of Rogers 4835 PCB help maintain device reliability and stability.
Why Choose Rogers 4835 Material Over Other High Frequency Materials?
Rogers 4835 material combines excellent electrical properties with stable mechanical properties to perform well in high-frequency environments. It has lower dielectric loss and better signal integrity than traditional fiberglass-reinforced boards such as FR-4 boards, making it suitable for demanding RF and microwave circuit designs. In addition, Rogers 4835 PCB material has long been proven in a wide range of industrial and commercial applications, ensuring its reliability and stability.