What is Rogers 4500 PCB?
RO4500 high frequency laminates are fully compatible with conventional FR-4 and high temperature lead free solder processing. These laminates do not require special treatment needed on traditional PTFE-based laminates for plated through-hole preparation. The resin systems of RO4500 dielectric materials provide the necessary properties for ideal antenna performance. This product series is an affordable alternative to more conventional antenna technologies, thus allowing designers to maximize the price and performance of their antennas.
Features
- Dielectric constant (Dk) range of 3.3 to 3.5 +/- 0.08
- Dissipation factor range of 0.0020 to 0.0037
- Available in large panel sizes
Benefits
- Excellent passive inter-modulation (PIM) with LoPro® copper foil
- Improved mechanical rigidity over PTFE
- CTE similar to that of copper, reducing stress in PCB antenna
Rogers 4500 PCB Manufacturer.”Rogers 4500 PCB Manufacturer” refers to a company specializing in the production of PCBs using Rogers 4500 series materials. They excel in manufacturing high-performance circuit boards known for their exceptional electrical properties and reliability in demanding applications like aerospace, telecommunications, and medical devices.
Rogers 4500 PCB is an excellent printed circuit board (PCB) widely used in high-frequency and high-speed electronic equipment. It uses 4500 series materials developed by Rogers Corporation, which are known for their excellent electrical properties and excellent thermal performance. Rogers 4500 PCBs demonstrate outstanding performance and reliability in modern electronics, particularly in wireless communications, radio frequency (RF) circuits, and microwave applications.
Rogers 4500 material has several key properties that make it ideal for high-frequency electronic designs. First, its low dielectric loss is one of its distinctive features. Low loss coefficient means less energy loss during signal transmission, helping to maintain signal clarity and strength. This is crucial for high-frequency, high-speed data transmission and microwave signal processing, and can effectively reduce distortion and noise in signal transmission.
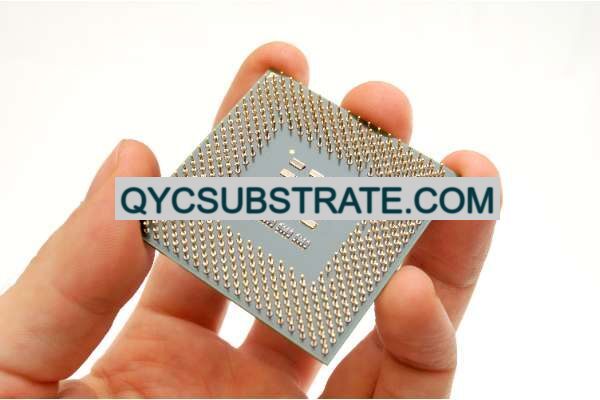
Rogers 4500 PCB Manufacturer
Secondly, Rogers 4500 PCB has a stable dielectric constant. This feature ensures that the signal transmission speed and waveform remain stable at different frequencies, helping to maintain the reliability and consistency of the circuit. In complex circuit layout and design, a stable dielectric constant can reduce signal delay and phase offset, improving system performance and response speed.
In addition, Rogers 4500 material is also known for its excellent dimensional stability. This means that the physical size and shape of the PCB board changes less during temperature changes or long periods of operation. This is important for applications that require high accuracy and stability, especially in electronic equipment at microwave frequencies and high temperature environments, to maintain circuit performance and reliability.
Rogers 4500 PCB is widely used in many high-tech fields. It is commonly found in communications infrastructure, satellite communications systems, radar technology, medical electronics, and aerospace technology. In these fields, circuit boards are required to transmit complex signals and data stably and efficiently to support high-speed data processing, precision control and long-distance communication.
Its advantage is that it can not only meet the technical requirements of high-frequency and high-speed signal transmission, but also maintain stable electrical performance in extreme environments. For example, the excellent thermal management capabilities of Rogers 4500 PCB enable it to effectively disperse and handle the heat generated in the circuit, helping to extend the service life of the equipment and improve the reliability of the system.
In summary, Rogers 4500 PCB has become an indispensable part of high-frequency and high-speed electronic design due to the excellent performance, stability and reliability of the material. Its low dielectric loss, stable dielectric constant and excellent dimensional stability make it widely used in modern communications, radio frequency and microwave technologies, providing powerful tools and solutions for electronic engineers and equipment manufacturers.
These characteristics and application scenarios demonstrate the key role of Rogers 4500 PCB in technological innovation and improvement of electronic product performance, providing a solid foundation for the development and advancement of future electronic equipment.
The types of Rogers 4500 PCB
When it comes to high frequency and high speed applications, Rogers 4500 PCB is particularly important as an excellent printed circuit board material for different types of designs and application needs. The following is a detailed introduction to the various types of Rogers 4500 PCB:
Rogers 4500 PCB is a versatile printed circuit board material that can be designed as single, dual or multi-layer boards depending on the needs of a specific application. These different types of PCBs differ in structure and functionality, so there are several factors to consider when selecting and designing them.
Single-layer Rogers 4500 PCBs consist primarily of one substrate and are suitable for simple circuit designs and cost-sensitive applications. This type of PCB has a simple structure and low manufacturing cost, and is suitable for some basic electronic equipment and consumer products. Although the circuit layout of a single-layer PCB is relatively simple, it can still provide good performance and stability, especially in applications that do not require complex signal processing or high-density component mounting.
The dual-layer Rogers 4500 PCB contains two layers of copper foil and a dielectric layer and is widely used in applications requiring more complex circuit layouts and higher levels of integration. This type of PCB can provide higher circuit density, allowing designers to implement more functions and components in a limited space. Double-layer PCB is usually used in industrial control, automotive electronics, wireless communications and other fields, and can support more complex signal transmission and data processing requirements.
A multilayer Rogers 4500 PCB is a complex structure consisting of three or more conductive layers stacked together with multiple dielectric layers. This design can support the most complex circuit layouts and highest integration requirements. Multilayer PCBs are widely used in communications infrastructure, satellite communications, medical equipment and other fields, enabling complex signal processing, data transmission and power management. By precisely controlling the conductive paths and signal spacing of each layer, multilayer PCBs can effectively reduce electromagnetic interference (EMI) and signal crosstalk, improving overall performance and reliability.
In communications infrastructure, different types of Rogers 4500 PCBs are widely used in base station antenna systems, RF front-end modules, and microwave communications equipment. Single-layer PCBs can be used for simple power amplifiers or low-frequency signal processing circuits, while double- and multi-layer PCBs can support more complex RF designs and high-speed data transmission needs. In the fields of satellite communications and medical equipment, the ability of multi-layer Rogers 4500 PCBs is to support sophisticated control and monitoring systems, ensuring data accuracy and stability.
Overall, the different types of Rogers 4500 PCBs can meet the different requirements for performance, reliability and cost-effectiveness of various electronic products. Design engineers need to select the most appropriate PCB type based on the characteristics and needs of the specific application to ensure optimization of circuit design and high quality of the final product.
The advantages of Rogers 4500 PCB
When it comes to the advantages of Rogers 4500 PCB, it is mainly due to its superior performance in high frequency characteristics, low loss and thermal performance. Here’s a detailed explanation:
The material used in the Rogers 4500 PCB has excellent high-frequency properties, making it outstanding in applications requiring high-speed data transmission and precision signal processing. High-frequency characteristics mainly refer to the low dielectric loss and stable dielectric constant of the material. The lower the dielectric loss, the less energy the signal loses during transmission, thereby maintaining the strength and integrity of the signal. Rogers 4500 PCB can effectively reduce signal distortion and ensure reliable transmission and accurate processing of high-frequency signals.
Rogers 4500 PCB significantly reduces dielectric losses compared to traditional FR-4 boards. FR-4 materials may produce high signal attenuation and losses in high-frequency environments, and the superior design and material selection of Rogers 4500 PCB effectively reduce these losses. The low-loss characteristics make it particularly suitable for high-speed data transmission and complex signal processing, such as the application requirements in 5G communications, RF front-end equipment, and microwave applications.
Rogers 4500 material has excellent thermal conductivity and stable thermal properties to effectively manage heat in circuits. In applications with high power density and long operating times, heat buildup can negatively impact circuit performance. Through the selection of materials with high thermal conductivity, Rogers 4500 PCB is able to effectively dissipate heat, maintaining circuit stability and long-term reliability.
Due to its excellent high-frequency characteristics, low loss and stable thermal performance, Rogers 4500 PCB is widely used in various high-end electronic equipment and systems. Especially in fields such as communication infrastructure, satellite communications, medical electronics, radar systems, and aerospace technology, PCBs have extremely high requirements for high performance and reliability. Rogers 4500 PCB meets these stringent requirements and operates reliably in complex environments.
Taken together, the advantages of Rogers 4500 PCB in terms of high frequency characteristics, low losses and thermal performance make it an ideal solution for select high performance electronic applications. By using advanced materials and exquisite manufacturing processes, it is able to play a key role in modern electronic devices, supporting the needs of high-speed data transmission and complex signal processing.
How to Design a Rogers 4500 PCB?
Designing a Rogers 4500 PCB requires precise planning and in-depth technical understanding to ensure the final circuit design will perform well in high-frequency and high-speed applications. The following are key steps and considerations in the design process:
First, the designer must fully understand the properties of Rogers 4500 material. Rogers 4500 material is known for its low dielectric loss and stable dielectric constant, properties that are critical for high-frequency circuits. In the early stages of circuit layout, engineers need to use professional CAD software, such as Altium Designer or Cadence Allegro, to accurately lay out circuit components and signal paths. Ensuring that the signal transmission path is as short as possible can significantly reduce signal delay and loss and improve circuit performance and stability.
Secondly, considering the special requirements of high-frequency applications, electromagnetic compatibility (EMC) principles need to be followed in the design. This means reducing the possibility of electromagnetic interference in circuit layout and design to prevent signal crosstalk and radiated interference. Through measures such as reasonable wiring, use of shielding technology, and ground wire planning, electromagnetic interference can be effectively managed and controlled to ensure the stability and reliability of the circuit in a complex electromagnetic environment.
Ultimately, selecting the proper manufacturing process is critical to the performance and quality of your Rogers 4500 PCB. Modern manufacturing processes such as surface mount technology (SMT) and multi-layer stacking technology can provide highly precise component mounting and signal lamination, which is especially important for complex circuit designs. SMT technology enables precise mounting of small-sized components, while multi-layer stacking technology can minimize circuit board space occupation and improve circuit layout flexibility and performance.
In summary, designing a Rogers 4500 PCB requires not only a deep understanding of the effects of material properties and circuit layout, but also strict adherence to best practices and manufacturing standards for high-frequency circuit design. Through reasonable design process and meticulous technical implementation, it can be ensured that the final product has excellent electrical performance, stability and reliability, and is suitable for a wide range of high-demand application scenarios in the fields of communications, radar, medical and aerospace.
Why use ceramic Rogers 4500 PCB over other boards?
During the design and manufacturing of electronic devices, selecting the appropriate printed circuit board (PCB) material is critical to ensuring device performance and reliability. In specific application scenarios, such as high-temperature environments and high-frequency signal transmission, ceramic PCBs (such as alumina ceramics) have significant advantages over traditional fiberglass reinforced boards (FR-4 boards).
First, ceramic PCB materials have higher thermal conductivity. In high-power-density applications, circuit boards can accumulate large amounts of heat, and ceramic PCBs can effectively transfer heat away from critical electronic components and circuits quickly, ensuring stable operation of the device. In contrast, the thermal conductivity of FR-4 board materials is low, which can lead to heat buildup and overheating of circuit components, affecting the performance and life of the device.
Secondly, ceramic PCBs have better mechanical stability. In environments with high vibration or mechanical shock, ceramic PCBs are better able to resist stress and distortion, maintaining the structural integrity of the board. This is particularly important for some extreme industrial environments or aerospace applications, which require electronic equipment to operate stably for a long time under harsh conditions.
In addition, ceramic PCBs have a low dielectric constant, which is one of their important advantages in high-frequency signal transmission. The dielectric constant affects the speed and loss of signals propagating through the circuit board. The low dielectric constant of ceramic PCB means less signal transmission loss and lower signal distortion, maintaining high signal clarity and accuracy. This makes ceramic PCBs ideal for radio frequency (RF) and microwave circuit designs, especially in applications where signal interference and noise need to be tightly controlled.
In summary, choosing ceramic PCBs over other types of PCBs has significant advantages in applications involving high-temperature environments and high-frequency signal transmission. Its high thermal conductivity, excellent mechanical stability and low dielectric constant enable it to maintain stable electrical performance under extreme conditions, ensuring efficient operation and long-term reliability of equipment. Therefore, for electronic device manufacturers and design engineers who require high performance and reliability, ceramic PCBs are a technology choice that cannot be ignored, capable of meeting complex and challenging application requirements.
What is the Rogers 4500 PCB Fabrication Process?
Manufacturing Rogers 4500 PCBs is a precise and complex process involving multiple process steps to ensure the final product meets high standards of design requirements and application needs. The following is a detailed process description of manufacturing the Rogers 4500 PCB:
First, the manufacturing process begins with the material selection and pre-processing stages. During the selection phase, engineers select the appropriate Rogers 4500 material based on specific circuit design and application needs. Rogers 4500 Series materials are known for their excellent electrical and thermal properties and are suitable for high frequency and high speed applications. In the pre-treatment stage, the surface of the material needs to be cleaned and smoothed to ensure that subsequent processes can be carried out on a clean, flat substrate.
Next comes the lamination process, which is one of the core steps in PCB manufacturing. In the lamination process, layers of circuit designs and materials are precisely stacked together to form a complete circuit board structure. Rogers 4500 PCBs can be single-layer, double-layer or multi-layer boards, depending on the design requirements. These layers are cured through a thermal pressure process of high temperature and pressure, ensuring a strong bond between the layers and the stability of the material.
This is followed by the drilling and electroless copper plating stages. During the PCB manufacturing process, holes need to be opened at predetermined locations through a precise drilling process to subsequently form conductive paths on the circuit board. After drilling is completed, the surface of the circuit board will be electroless copper plating. This step is designed to form a conductive path at the drilled area to ensure that various parts of the circuit can be connected and transmit signals smoothly.
Next comes the patterning step, which is one of the keys to manufacturing PCBs. The designed circuit pattern is transferred to the surface of the PCB through photolithography or etching. This process involves the use of photosensitizers to precisely transfer circuit patterns to the surface of copper foil, creating conductive traces and component mounting areas.
Finally comes the metallization and surface treatment stage. In the metallization process, a conductive layer is formed on the patterned conductive path by depositing metal material (such as tin-lead alloy or metallization material). This layer ensures the conductivity and connection reliability of the circuit. Surface treatment includes coating with a protective layer or surface gold plating to improve the durability and oxidation resistance of the PCB and ensure its long-term stability during use.
Strict control of parameters and quality inspection are crucial throughout the entire manufacturing process. Each step of the process requires compliance with strict standards and quality control procedures to ensure the consistency and performance stability of each Rogers 4500 PCB. These measures not only ensure the quality of the product, but also ensure the reliability and durability of the PCB in various complex application environments.
Although the manufacturing process of Rogers 4500 PCB is complicated, through precise process control and efficient technical support, it can meet the strict requirements of high performance and reliability of modern electronic equipment, and is widely used in communications, medical, aerospace and other industries.
The application of ceramic Rogers 4500 PCB
Rogers 4500 PCB is a printed circuit board designed for high-frequency and high-speed electronic applications and is widely used in several key areas for its excellent performance and reliability. The following are its specific applications in different industries:
Rogers 4500 PCBs play a key role in modern communications infrastructure. These facilities need to be able to handle large amounts of data and ensure stable signal transmission. Rogers 4500 PCB supports high-frequency data transmission and complex communication protocols through its low dielectric loss and superior signal integrity. From base stations to network centers, these PCBs help keep communications networks running efficiently.
Satellite communication systems rely on high-performance electronic equipment to achieve long-distance data transmission and wide-area coverage. Rogers 4500 PCBs are widely used in satellite receivers, transmitters and data processing units because of their ability to withstand high-frequency interference and thermal changes in extreme environmental conditions. These PCBs not only ensure stable transmission of signals but also enable long-term reliable operation in satellite orbits.
Radar systems require high accuracy and fast response capabilities to detect and track targets. Rogers 4500 PCBs play key roles in radar antennas, signal processing modules and control units. Its excellent electrical performance and stable dimensional characteristics support radar systems working in complex electromagnetic environments, ensuring data accuracy and real-time performance.
Medical devices require highly reliable and precise electronic components to support patient monitoring, diagnosis and treatment. Rogers 4500 PCB is widely used in high-frequency electronic medical equipment such as MRI (magnetic resonance imaging), CT scanners and medical communication systems. Its stable signal transmission and high temperature resistance ensure the long-term stable operation of the equipment in hospitals and clinical environments.
The aerospace industry places extremely demanding demands on electronic equipment, which must be able to operate reliably under extreme conditions of temperature, radiation and mechanical vibration. Rogers 4500 PCBs play an important role in flight control systems, navigation instruments and satellite payloads because of their ability to withstand the extreme environmental challenges faced by spacecraft and maintain efficient data transfer and processing capabilities.
In summary, Rogers 4500 PCB has demonstrated its irreplaceable role in communications, medical, aerospace and other fields with its excellent high-frequency characteristics, low loss and stable thermal performance. As the industry’s first choice, it provides a solid foundation for the development of modern electronic technology, ensuring reliable operation and long-term stability of equipment in various complex and extreme environments.
FAQs
What frequency ranges are Rogers 4500 PCB suitable for?
Rogers 4500 PCBs are primarily designed for use in a wide range of high frequency applications, typically covering frequency ranges from a few hundred megahertz to several gigahertz. This makes it very suitable for 5G communications, radio frequency front-end equipment, microwave communication systems and other application scenarios that require high-frequency transmission and precise signal processing. The superior electrical characteristics and stability of Rogers 4500 PCB ensure excellent performance in these high-speed data transmission environments.
How is the thermal management of the Rogers 4500 PCB?
Rogers 4500 PCB material has excellent thermal conductivity and thermal stability to effectively manage heat in circuits. This makes it particularly suitable for applications requiring high power density and long operation times. In high-frequency and high-speed circuits, heat buildup can have a negative impact on signal stability and circuit life. Therefore, the good thermal management capabilities of Rogers 4500 PCB help maintain device reliability and stability.
Why choose Rogers 4500 material over other high frequency materials?
Rogers 4500 material combines excellent electrical properties with stable mechanical properties to perform well in high-frequency environments. It has lower dielectric loss and better signal integrity than traditional fiberglass-reinforced boards such as FR-4 boards, making it suitable for demanding RF and microwave circuit designs. In addition, Rogers 4500 PCB material has long been proven in a wide range of industrial and commercial applications, ensuring its reliability and stability.
What is the manufacturing process of Rogers 4500 PCB?
Manufacturing Rogers 4500 PCBs requires multiple process steps to ensure the final product meets design requirements and standards. First, select the appropriate material and perform pre-treatment to ensure the surface of the board is smooth and clean. Next comes the lamination process, where the layers of circuit design are stacked together and cured through heat pressure. This is followed by drilling, electroless copper plating, and patterning to create conductive paths and component mounting areas on the board. The last step is metallization and surface treatment to ensure the connection reliability and durability of the circuit board. The entire manufacturing process requires strict control of parameters and quality inspection to ensure the consistency and performance stability of each PCB.