Thick Film Ceramic PCBs Manufacturer.A leading manufacturer of Thick Film Ceramic PCBs, specializing in high-performance solutions for demanding applications. Our advanced technology ensures excellent thermal management, high reliability, and superior conductivity. We cater to various industries, including aerospace, automotive, and medical devices, offering customized designs and rapid prototyping. With a commitment to quality and innovation, we deliver robust, durable PCBs that meet the highest industry standards.
What is a Thick Film Ceramic PCB?
Thick Film Ceramic PCBs are a type of circuit board where conductive, resistive, and dielectric materials are deposited as thick films onto a ceramic substrate. Unlike thin film ceramic PCBs, which use a very thin layer of conductive material, thick film ceramic PCBs apply a thicker layer, usually in the range of several micrometers, to create the circuit patterns. This method is advantageous for producing robust and durable circuits that can handle higher power levels and harsh environmental conditions.
The ceramic substrate used in thick film PCBs typically includes materials like alumina (Al₂O₃), which provides excellent thermal stability, electrical insulation, and mechanical strength. The thick film process involves screen printing the conductive pastes onto the ceramic substrate, followed by firing at high temperatures to bond the materials permanently. This creates a reliable and long-lasting circuit board that performs well in demanding applications.
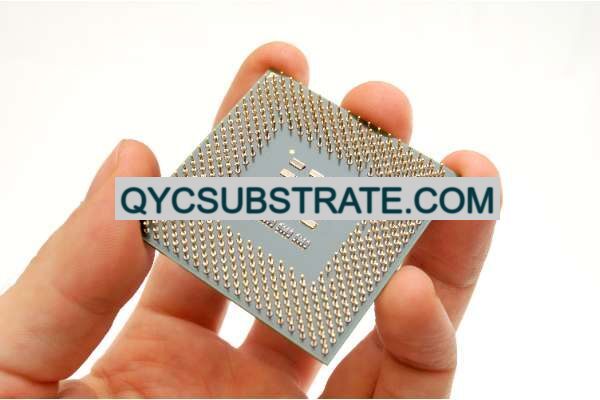
Thick Film Ceramic PCBs Manufacturer
The Types of Thick Film Ceramic PCBs
Thick Film Ceramic PCBs come in various configurations, each tailored to meet different application requirements.
Single-layer thick film ceramic PCBs consist of a single layer of thick film circuits printed onto a ceramic substrate. These are commonly used in simpler electronic designs where robustness and durability are essential, such as in power electronics and sensors.
Multi-layer thick film ceramic PCBs involve stacking multiple layers of ceramic substrates, each with its own circuit patterns. The layers are interconnected through vias, allowing for more complex circuit designs while maintaining the advantages of thick film technology. This design is useful in applications where high-density interconnections are needed.
Hybrid thick film ceramic PCBs combine thick film technology with other types of circuits or substrates, such as thin film or metal-based PCBs. This hybrid approach allows for customized performance characteristics, providing the best of both worlds in terms of durability and precision.
Customized thick film ceramic PCBs are designed to meet specific application needs, including unique circuit layouts, integrated passive components, or specialized thermal management features. These customized designs are used in advanced electronic systems where standard solutions do not suffice.
The Advantages of Thick Film Ceramic PCBs
Thick Film Ceramic PCBs offer several notable advantages, particularly in terms of durability and power handling. The thicker conductive layers allow these PCBs to carry higher currents and voltages, making them ideal for power electronics and other high-power applications. The robust nature of the thick film materials also means that these PCBs can withstand harsh environments, including extreme temperatures, moisture, and chemical exposure.
The use of ceramic substrates provides excellent thermal management, as ceramics have high thermal conductivity and can efficiently dissipate heat generated by the circuit. This is crucial in applications where maintaining low operating temperatures is essential for reliability and performance.
Additionally, thick film ceramic PCBs are highly customizable. The screen printing process allows for the easy integration of resistors, capacitors, and other passive components directly onto the PCB, reducing the need for additional components and simplifying the overall design. This integration leads to more compact and efficient circuits, particularly in high-density applications.
The long-term reliability of thick film ceramic PCBs is another significant advantage. The materials used in these PCBs are resistant to wear and degradation over time, ensuring stable performance even after prolonged use. This makes them a preferred choice for industrial, automotive, and aerospace applications where long-term durability is critical.
How to Design a Thick Film Ceramic PCB?
Designing a Thick Film Ceramic PCB involves several key steps that are essential for creating a reliable and efficient circuit. The process begins with defining the application requirements, including electrical specifications, environmental conditions, and mechanical constraints. This initial step is critical to ensure that the final design will meet the intended performance criteria.
Next, the appropriate ceramic substrate material and thick film pastes are selected based on the application’s needs. The choice of materials influences the PCB’s thermal performance, electrical characteristics, and durability. Once the materials are selected, a detailed circuit schematic is created, outlining the components and their connections.
The PCB layout is then designed using specialized software, taking into account the thickness of the conductive layers, the placement of components, and the routing of connections. This layout must be optimized for the thick film process, ensuring that the circuit paths are robust enough to handle the required currents and voltages.
The next step is the screen printing of the thick film pastes onto the ceramic substrate. This process involves applying the conductive, resistive, and dielectric materials in layers, followed by high-temperature firing to permanently bond the materials to the substrate. After the printing and firing processes are completed, the PCB undergoes testing to ensure that all circuits are functioning correctly and meet the required specifications.
Finally, the assembled PCB is subjected to a series of inspections, including electrical testing, dimensional verification, and environmental testing, to confirm that it meets the design criteria and is ready for use in its intended application.
Why Use Thick Film Ceramic PCBs Over Other Boards?
Thick Film Ceramic PCBs offer distinct advantages that make them preferable over other types of circuit boards, particularly in applications requiring high durability, power handling, and environmental resistance. One of the primary reasons for choosing thick film ceramics is their ability to handle higher power levels without compromising performance. The thicker conductive layers are more robust and can carry higher currents and voltages, making them ideal for power electronics and high-frequency circuits.
The ceramic substrate used in thick film PCBs provides excellent thermal management, which is critical in high-power applications. The high thermal conductivity of ceramics allows for efficient heat dissipation, preventing overheating and ensuring long-term reliability of the circuit.
Another advantage is the environmental resilience of thick film ceramic PCBs. These boards can withstand extreme temperatures, humidity, and exposure to chemicals, making them suitable for use in harsh environments such as industrial automation, automotive electronics, and aerospace systems.
Thick film ceramic PCBs are also highly customizable, allowing for the integration of various passive components directly onto the board. This capability simplifies the overall circuit design, reduces the number of discrete components, and enhances the reliability of the final product.
Overall, the combination of high power handling, excellent thermal management, environmental resilience, and customizability makes thick film ceramic PCBs a superior choice for demanding electronic applications.
What is the Thick Film Ceramic PCB Fabrication Process?
The fabrication process of Thick Film Ceramic PCBs involves several specialized steps that ensure the creation of durable and high-performance circuit boards. The process begins with the preparation of the ceramic substrate, typically made from materials like alumina (Al₂O₃), known for its excellent thermal and electrical properties.
Once the substrate is prepared, the thick film materials are applied using a screen printing process. This involves applying conductive, resistive, and dielectric pastes onto the ceramic surface through a patterned screen. Each layer is printed and then fired in a high-temperature furnace to bond the materials to the ceramic substrate. The firing process ensures that the thick film layers are permanently adhered and that the electrical properties of the materials are stabilized.
After the printing and firing of all necessary layers, the PCB is inspected for accuracy and quality. This includes verifying the thickness and uniformity of the thick film layers, as well as checking for any defects or misalignments. If necessary, additional surface finishing processes, such as plating or coating, are applied to enhance the PCB’s durability and performance.
The final step in the fabrication process involves the assembly of components onto the thick film ceramic PCB. This is done with precision to ensure proper placement and reliable electrical connections. The assembled PCB is then subjected to rigorous testing, including electrical testing to verify connectivity and performance, as well as environmental testing to assess its resilience under various conditions.
The entire fabrication process is carefully controlled to produce thick film ceramic PCBs that meet the stringent requirements of high-power and high-reliability applications.
The Application of Thick Film Ceramic PCBs
Thick Film Ceramic PCBs are widely used in a variety of demanding applications due to their robustness, high power handling capabilities, and environmental resilience. They are commonly found in industrial automation systems, where they are used to control and monitor machinery and equipment. The durability and high power handling of thick film ceramics make them ideal for these applications, where reliability is critical.
In the automotive industry, thick film ceramic PCBs are used in engine control units, sensors, and other electronic components that must withstand high temperatures, vibrations, and exposure to harsh chemicals. The ability of thick film ceramics to perform reliably in these challenging conditions makes them a preferred choice for automotive electronics.
Aerospace applications also benefit from the use of thick film ceramic PCBs. In this industry, these PCBs are used in avionics, communication systems, and other critical electronic systems that must operate under extreme conditions, including high altitude, temperature fluctuations, and intense vibration.
Thick film ceramic PCBs are also used in power electronics, such as power converters, inverters, and amplifiers, where their ability to handle high currents and voltages is essential. The effective thermal management provided by the ceramic substrate ensures that these devices operate efficiently and reliably.
Medical devices are another area where thick film ceramic PCBs are commonly used. Their high reliability and ability to withstand sterilization processes make them suitable for critical medical equipment, including diagnostic instruments and implantable devices.
In summary, the applications of thick film ceramic PCBs span a wide range of industries, including industrial automation, automotive, aerospace, power electronics, and medical devices. Their unique properties make them an ideal choice for any application requiring durability, power handling, and environmental resistance.
FAQs
What are Thick Film Ceramic PCBs?
Thick Film Ceramic PCBs are circuit boards that use a ceramic substrate with conductive, resistive, and dielectric materials deposited as thick films. They are known for their durability, power handling, and environmental resilience.
What types of Thick Film Ceramic PCBs are available?
Types include single-layer, multi-layer, hybrid, and customized thick film ceramic PCBs, each designed for specific performance and design needs.
What are the advantages of Thick Film Ceramic PCBs?
Advantages include high power handling, excellent thermal management, environmental resilience, and the ability to integrate passive components directly onto the PCB.
How is a Thick FilmCeramic PCB designed?
The design process involves defining requirements, selecting materials, creating schematics and layouts, printing and firing thick film materials, and verifying performance through testing.