What is Rogers TC600 PCB?
TC600 laminates best-in-class thermal conductivity and mechanical robustness enable printed circuit board (PCB) size reduction. The increased thermal conductivity provides higher power handling, reduces hot-spots and improves device reliability.
Features
- Dielectric constant (Dk) of 6.15
- High thermal conductivity of 1.0W/mK
- Stable Dk across wide temperature range of -75ppm/°C from -40°C to 140°C
- Low loss tangent of .002 at 10 GHz
- Low coefficient of thermal expansion on X,Y and Z axis (9, 9 and 35 ppm/°C)
Benefits
- Enables size reduction of PCB relative to lower Dk substrates
- Reduced heat generated through transmission line loss
- Improved processing and reliability
- CTE matches active components for low stress solder joints
Rogers TC600 PCB Manufacturer.Rogers TC600 PCB Manufacturer specializes in producing high-performance printed circuit boards using Rogers TC600 materials. Known for their excellent thermal conductivity and stability, these PCBs are ideal for demanding applications in telecommunications, aerospace, and defense. With cutting-edge technology and rigorous quality control, Rogers TC600 PCB Manufacturer ensures reliable and efficient solutions for advanced electronic systems.
Rogers TC600 PCB is a high-performance printed circuit board (PCB) made from Rogers Corporation’s TC600 material. This material is known for its excellent thermal conductivity and excellent electrical properties, making it particularly suitable for high-frequency and high-power applications. Rogers TC600 PCB material has extremely low dielectric losses and excellent thermal stability, allowing it to perform well in complex electronic designs.
Rogers TC600 PCB is designed to handle the needs of high power and high frequency applications. The excellent properties of this material give it broad application prospects in electronic design. First, the high thermal conductivity of Rogers TC600 material allows it to effectively dissipate heat and prevent circuit boards from overheating under high power conditions, thereby improving the reliability and service life of electronic equipment. Secondly, the low dielectric loss characteristics of TC600 materials ensure the integrity of signals in high-frequency transmission and reduce signal loss and distortion, which is particularly important for high-frequency communication equipment and high-speed digital circuits.
Additionally, the excellent thermal stability of Rogers TC600 PCB means it maintains excellent performance under extreme temperature conditions. This makes it excellent in fields such as aerospace, military electronics, radio frequency and microwave communications that require working in harsh environments. For example, in satellite communications systems, Rogers TC600 PCB can maintain stable performance in extreme temperatures and high radiation environments, ensuring the reliability of signal transmission.
The manufacturing process of Rogers TC600 PCB is also very delicate, ensuring that the material properties are fully utilized. During the design and manufacturing process, engineers need to pay special attention to the material’s characteristics to optimize circuit layout and thermal design to take full advantage of the TC600 material. Through reasonable design and high-quality manufacturing process, Rogers TC600 PCB can meet the needs of various complex electronic applications.
In summary, the Rogers TC600 PCB is a high-performance, high-reliability printed circuit board that is particularly suitable for high-frequency and high-power applications. Its excellent thermal conductivity, low dielectric loss and excellent thermal stability enable it to perform well in complex electronic designs and is widely used in communication equipment, military electronics, aerospace and other fields. By using Rogers TC600 PCBs, engineers can design electronic devices with higher performance and greater reliability to meet growing technology demands.
The types of Rogers TC600 PCB
Rogers TC600 PCB mainly has the following types, each type is designed according to its specific structure and application requirements to meet different circuit and system requirements:
A single-layer board is the most basic form of PCB and contains only one conductive layer. This type of Rogers TC600 PCB is typically used in simple circuit designs such as analog and digital signal processing at low frequencies. Due to its simple structure, the manufacturing cost is low and it is easy to design and maintain. Single-layer boards are suitable for applications that require stable electrical performance and low heat dissipation requirements.
A double-layer board has two conductive layers connected by vias. This type of Rogers TC600 PCB can support more complex circuit designs, providing more routing space and flexibility. Double-layer boards have improved signal integrity and heat dissipation performance compared with single-layer boards, and are suitable for medium-complexity high-frequency circuits, such as radio frequency amplifiers and antenna circuits.
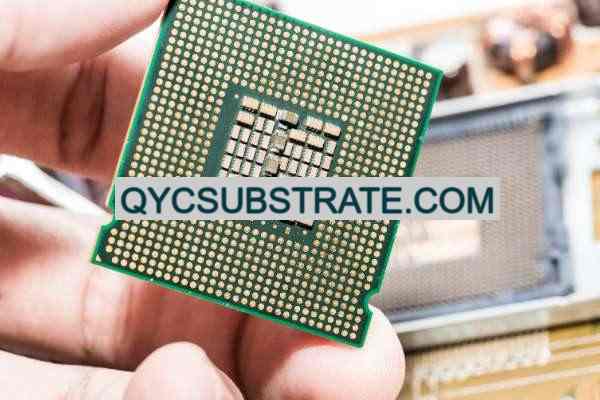
Rogers TC600 PCB Manufacturer
Multilayer boards contain three or more conductive layers and are manufactured through internal lamination technology. This type of Rogers TC600 PCB is designed for use in high-complexity and high-density circuits such as high-speed signal processing, microwave circuits, and RF modules. Multilayer boards enable higher electrical performance and better thermal management, making them ideal for high-power and high-frequency applications.
The soft-hard board is composed of a combination of flexible circuits and rigid circuits. This type of Rogers TC600 PCB offers greater design flexibility, enabling complex three-dimensional circuit layouts within limited space. Rigid-flex boards work especially well in applications that require high reliability and mechanical stability, such as aerospace and medical equipment.
Ceramic filled PCB uses ceramic filler materials to enhance the thermal conductivity and electrical performance of the substrate. This type of Rogers TC600 PCB is suitable for extreme temperature environments and high power density applications such as power amplifiers and high frequency filters. Ceramic-filled PCB provides excellent thermal dissipation and mechanical strength, ensuring stable operation under harsh conditions.
Rogers TC600 PCB materials are available in a variety of types and structural designs to meet the needs of different application scenarios, from simple low-frequency circuits to complex high-frequency and high-power systems, all providing excellent performance and reliability. These types of PCBs are widely used in fields such as wireless communications, aerospace, medical electronics, and high-performance computing.
The advantages of Rogers TC600 PCB
Rogers TC600 PCB offers several distinct advantages that make it stand out in high-performance and high-frequency applications. Here are the key benefits of Rogers TC600 PCB:
Rogers TC600 material is known for its excellent thermal conductivity properties. This highly thermally conductive material can effectively dissipate heat and ensure stable operation of circuits in high power density and high temperature environments. The Rogers TC600 PCB is ideal for applications that require strict thermal management, such as power amplifiers and RF microwave circuits.
Rogers TC600 PCB has extremely low dielectric loss (Df), which means it provides better signal integrity and less signal attenuation in high-frequency applications. Low dielectric loss is critical for high-frequency and high-speed circuits because it maintains signal clarity and transmission speed, reducing energy loss and heat generation.
The dielectric constant (Dk) of Rogers TC600 material is very stable and remains consistent even over a wide frequency range and varying temperatures. This stability is critical for designing circuits with high precision and reliability, ensuring they perform well under a wide range of operating conditions.
Rogers TC600 PCB also offers superior mechanical properties, including good impact resistance and peel strength. This allows it to withstand mechanical stress during manufacturing and assembly, reducing the rate of failure due to physical damage.
Rogers TC600 material meets environmental standards and its manufacturing process has a low environmental impact. In addition, this material has extremely high reliability and can maintain stable performance over long periods of operation, reducing the frequency of maintenance and replacement.
Due to its excellent electrical and thermal properties, Rogers TC600 PCB is widely used in wireless communications, radar systems, satellite technology, medical electronics and aerospace. These applications often require high frequency and high power circuits, and the Rogers TC600 PCB meets these stringent requirements.
To sum up, Rogers TC600 PCB has significant advantages in high-frequency and high-power applications due to its excellent thermal conductivity performance, low dielectric loss, stable dielectric constant, superior mechanical properties and high reliability. These properties make Rogers TC600 PCB the material of choice for electronics engineers designing complex and demanding circuits.
How to Design a Rogers TC600 PCB?
Rogers TC600 PCB offers several distinct advantages that make it popular for high-performance electronic applications. Here are its main advantages:
Rogers TC600 material is known for its high thermal conductivity, allowing it to dissipate heat efficiently. This is particularly important in high power density applications, ensuring that electronic components do not overheat during operation, thereby extending their service life and reliability. Efficient thermal management not only improves device performance but also reduces the risk of failure due to overheating.
Rogers TC600 PCB material has extremely low dielectric losses and a stable dielectric constant. These characteristics make it excellent in high-frequency applications, ensuring high-fidelity signal transmission and minimal signal attenuation. A stable dielectric constant also helps designers achieve consistent performance across temperature and frequency conditions, especially for RF and microwave circuits.
Rogers TC600 PCB material performs well at high temperatures and maintains stable performance in extreme environmental conditions. This makes it suitable for aerospace, military and other demanding applications. Its thermal stability not only ensures reliability under high-temperature operation, but also improves overall system safety.
Rogers TC600 PCB material has excellent mechanical strength and can resist external physical impact and mechanical stress. The high-strength material makes it less susceptible to damage during assembly and use, thereby increasing the durability and reliability of the product. This durability makes it equally effective in industrial and commercial applications.
The superior properties of Rogers TC600 PCB material allow for a high degree of flexibility in the design and manufacturing process. Designers have the flexibility to choose material thickness, number of layers, and other parameters based on specific application needs to optimize circuit performance. Flexible design capabilities enable it to meet the needs of various complex circuits.
Rogers TC600 PCB material is easy to process and compatible with traditional PCB manufacturing processes. This compatibility eliminates the need for special equipment and technology during the production process, reducing manufacturing costs and difficulty. The ease of processing makes it suitable for mass production, ensuring product consistency and quality.
Overall, Rogers TC600 PCB excels in high-frequency, high-power and demanding applications due to its superior thermal conductivity, excellent electrical characteristics, excellent thermal stability and high mechanical strength. Its design flexibility and compatibility further enhance its applicability and value in a variety of electronic designs.
Why use ceramic Rogers TC600 PCB over other boards?
In electronics design and manufacturing, selecting the appropriate printed circuit board (PCB) material is critical to the performance and reliability of the final product. Ceramic Rogers TC600 PCBs offer several significant advantages over other types of PCBs, making them more competitive for specific applications.
Ceramic Rogers TC600 PCB is known for its high thermal conductivity. This means it can dissipate heat more efficiently, maintaining circuit stability and reliability. In high-power applications, such as radio frequency (RF) and microwave devices, thermal management is a critical issue. The excellent thermal conductivity of ceramic materials can quickly conduct heat away, prevent overheating problems, and extend the service life of electronic components.
Rogers TC600 material has excellent electrical properties, especially in high frequency applications. Its low dielectric loss and stable dielectric constant make signal transmission more stable and efficient, reducing signal attenuation and distortion. This is critical for communications equipment, radar systems and other high-frequency circuits that require high accuracy and reliability.
Ceramic Rogers TC600 PCBs offer excellent mechanical stability, maintaining their structural integrity and performance stability in extreme temperatures and harsh environments. In contrast, traditional FR4 materials are prone to deformation and performance degradation in high-temperature environments. Ceramic materials, on the other hand, maintain their mechanical and electrical properties over a wide temperature range, making them excellent in aerospace, automotive electronics and military applications.
Ceramic Rogers TC600 PCB has excellent chemical resistance, meaning it maintains its performance and longevity when faced with chemicals, moisture, and other harsh environmental factors. Other types of PCBs, especially standard FR4 materials, can be attacked by chemicals, causing performance degradation and shortened service life. This durability of ceramic PCBs makes them excellent in industrial controls, medical equipment, and outdoor electronics.
Although ceramic materials are difficult to process, with the advancement of technology, the manufacturing process of ceramic Rogers TC600 PCB has gradually matured and can meet the needs of complex circuit design. In addition, ceramic PCBs can achieve complex circuit layouts and high-density integration of electronic components through precision machining and micromachining technology, which provides engineers with greater design flexibility.
In summary, choose ceramic Rogers TC600 PCB over other types of PCBs primarily because of its superior thermal management capabilities, superior electrical performance, mechanical stability, chemical resistance, and design flexibility. These properties give ceramic Rogers TC600 PCBs significant advantages in high frequency, high power and harsh environment applications, making them ideal for many demanding electronic designs.
What is the Rogers TC600 PCB Fabrication Process?
The manufacturing process of Rogers TC600 PCB is a precise and complex process designed to ensure that the final product meets the requirements of high-performance electronic devices. Here are its main steps:
Manufacturing a Rogers TC600 PCB begins with preparing the TC600 material, a high-performance substrate material with excellent thermal conductivity and electrical properties. The quality of material selection directly affects the performance and stability of the final PCB.
PCB manufacturing begins with the lamination pre-treatment stage, where the surface of the TC600 material needs to be cleaned and chemically treated to ensure the flatness and cleanliness of the material surface, laying the foundation for subsequent process steps.
Graphical design of PCB using CAD (Computer Aided Design) software. Designers draw circuit layout and connection paths on the surface of TC600 material based on circuit needs and performance requirements. This step is crucial as it determines the functionality and performance of the final PCB.
The next step in PCB manufacturing is to transfer the design pattern onto the TC600 material. This involves using photolithography to transfer the design onto a photosensitive coating, and chemical etching to remove unwanted copper foil to create the circuit pattern. Drilling operations are then performed to facilitate subsequent electrical connections.
After drilling is completed, the PCB surface is electroless copper plated. This step ensures that the circuit paths and connection points are conductive and corrosion-resistant, thereby increasing the reliability and longevity of the PCB.
The final stages of PCB manufacturing include metallization and final inspection. Metallized coatings protect circuits from the outside environment and provide additional mechanical support. The final inspection phase ensures that the PCB meets design specifications and customer requirements through electrical performance testing, visual inspection, and functional verification.
Rogers TC600 PCB’s manufacturing process combines advanced materials science and precision machining techniques to provide a reliable solution for high-frequency and high-performance applications. Through strict quality control and process flow, we ensure that each produced PCB can operate stably in complex electronic systems and meet the requirements of industry standards and customer expectations.
The application of ceramic Rogers TC600 PCB
Ceramic Rogers TC600 PCB is a high-performance printed circuit board widely used in modern electronic technology. Its unique material properties give it a variety of important application scenarios.
In the communications field, ceramic Rogers TC600 PCB is favored for its excellent high-frequency characteristics and low dielectric loss. It can support high-frequency signal transmission, maintain signal stability and reliability, and is suitable for the manufacturing of various base station equipment, antenna systems and satellite communication equipment. These applications have very stringent requirements for high frequency and high-speed data transmission, for which TC600 material is ideally designed.
In RF and microwave circuit designs, ceramic Rogers TC600 PCBs can effectively manage the transmission and reflection of electromagnetic waves, reducing signal loss and improving overall system performance. Its excellent thermal conductivity and stable dielectric properties make it the material of choice for radar systems, wireless LAN equipment (such as Wi-Fi routers), and various types of radar sensors.
Ceramic Rogers TC600 PCBs are particularly useful in high-frequency electronic devices that require a high degree of accuracy and stability. For example, in the fields of high-frequency radio frequency signal processing in medical equipment, safety detection equipment, and particle accelerators in scientific research, TC600 PCB can ensure the precise operation of circuits while resisting interference from the external environment.
In aerospace and defense, the high-temperature stability and exceptional durability of ceramic Rogers TC600 PCBs make them an integral part of flight control systems, navigation equipment, and communications systems. These systems have extremely high requirements for high performance, high reliability and long-term stability, and TC600 PCB can meet these stringent technical standards.
In summary, ceramic Rogers TC600 PCB is widely used in communication technology, radio frequency and microwave circuits, high-frequency electronic equipment, and aerospace and defense technology through its excellent material properties. Its application in modern high-tech electronic equipment not only promotes technological progress, but also improves the performance and reliability of the overall system.
These application areas demonstrate the important role of TC600 PCB in a variety of key areas, heralding its continued development and broad application prospects in future high-frequency electronic equipment.
FAQ
What application scenarios is Rogers TC600 PCB suitable for?
Rogers TC600 PCB is particularly suitable for high frequency and high power density applications due to its excellent thermal conductivity properties and low dielectric loss. This includes radio frequency communications, microwave technology, radar systems, and industrial electronic equipment that require a high degree of stability and reliability.
What are the thermal management capabilities of the Rogers TC600 PCB?
Rogers TC600 PCB’s material, TC600, has excellent thermal conductivity properties, effectively dispersing and transferring heat. This makes it superior in high power density designs, maintaining stable operation of circuit components.
What are the advantages of TC600 PCB compared to other high-frequency PCB materials?
The main advantages of Rogers TC600 PCB compared to other high-frequency PCB materials, such as FR4, are its extremely low dielectric losses and excellent thermal stability. This makes it more reliable in scenarios that require high-frequency signal transmission and long-term operation.
How do you ensure the design and manufacturing quality of your Rogers TC600 PCB?
When designing a Rogers TC600 PCB, professional CAD software should be used to ensure that the circuit layout meets high-frequency requirements and takes into account the thermal conductivity properties of the material. During the manufacturing process, Rogers Corporation’s recommendations and processes are strictly followed for material pre-processing, lamination, molding and other steps to ensure the quality and performance of the final product.
What is the lifespan of a Rogers TC600 PCB?
Properly designed and manufactured, Rogers TC600 PCBs provide long-term performance and reliability, especially in harsh environmental conditions. Regular maintenance and inspections also help extend their service life.