Rigid-Flex PCB Manufacturer,A Rigid-Flex PCB Manufacturer specializes in crafting printed circuit boards (PCBs) that combine both rigid and flexible components, offering versatile solutions for diverse electronic applications. Employing advanced techniques, they integrate rigid sections with flexible substrates, enabling intricate designs that conserve space and enhance durability. With meticulous attention to detail, these manufacturers ensure precise alignment and robust construction, crucial for demanding environments such as aerospace, medical devices, and consumer electronics. Their expertise lies in producing innovative PCBs that seamlessly adapt to complex layouts, facilitating the seamless integration of electronic components while optimizing performance and reliability.
As electronic devices become increasingly miniaturized and complex, Rigid-Flex PCB technology is becoming increasingly important. Traditional rigid circuit boards have limitations in meeting the needs of modern electronic products, and the emergence of Rigid-Flex PCB makes up for this shortcoming. It combines the advantages of rigid and flexible parts, not only meeting the layout needs of complex electronic devices, but also improving reliability and durability. This article will delve into various aspects of Rigid-Flex PCB technology to help you better understand and apply this key technology.
What is Rigid-Flex PCB?
Rigid-Flex PCB (rigid flexible circuit board) is a unique electronic manufacturing technology that combines a rigid circuit board (Rigid PCB) with a flexible circuit board (Flex PCB) to form a whole. This circuit board structure contains both rigid (Rigid) and flexible (Flex) parts. The rigid part is usually composed of glass fiber reinforced epoxy resin, while the flexible part is made of flexible polyimide (PI) or polyethylene. Made of amide (PET) base material.
The design principle of Rigid-Flex PCB is to interconnect rigid and flexible parts to form a continuous circuit board structure. By adding flexible circuit boards at the edges of rigid areas, the board can be folded, bent or bent in devices with less space constraints. This design flexibility greatly improves the space utilization of electronic devices, making it possible to integrate more functions into miniaturized products.
Rigid parts are usually used to support and fix electronic components, while flexible parts are used to connect various rigid parts to make the entire system more stable and durable. This hybrid structure not only reduces the number of connecting wires in electronic equipment, but also improves the reliability and anti-interference capabilities of the system because fewer connection points and joints are reduced, reducing the risk of failure.
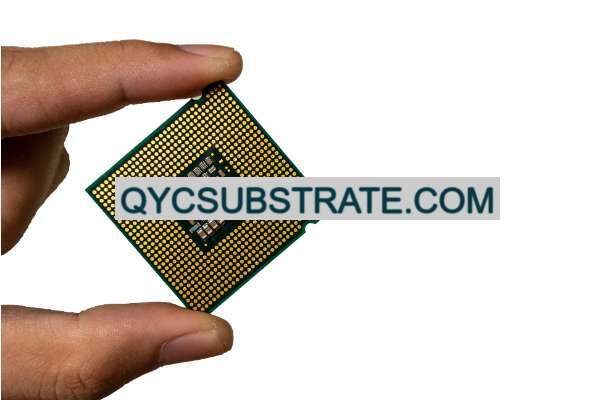
Rigid-Flex PCB Manufacturer
Overall, Rigid-Flex PCB technology plays a vital role in the design of electronic equipment. It not only helps engineers overcome space constraints and achieve more complex designs, but also improves the reliability and stability of the system. With the continuous advancement of technology, the application scope of Rigid-Flex PCB technology is also constantly expanding, becoming one of the important innovations in the field of modern electronic manufacturing.
The types of Rigid-Flex PCB
Rigid-Flex PCB is a circuit board technology that combines rigid and flexible parts to provide more design flexibility and space utilization for electronic devices. In the field of Rigid-Flex PCB, there are many types and designs to choose from to meet different application needs. Below is a detailed description of the main types of Rigid-Flex PCB:
Single-sided Rigid-Flex PCB
Single-sided Rigid-Flex PCB is one of the simplest types, where one side of the board has a rigid structure and the other side is flexible. This design is suitable for space-constrained applications such as mobile devices or medical devices, and its structure is simple and easy to manufacture.
Double-sided Rigid-Flex PCB
Double-sided Rigid-Flex PCB has two rigid layers on either side of the flexible material. This design allows for more complex circuit layouts in a smaller space and provides higher circuit density. Double-sided Rigid-Flex PCB is commonly used in fields such as industrial control, automotive electronics and communication equipment.
Multilayer Rigid-Flex PCB
Multilayer Rigid-Flex PCBs feature multiple rigid and flexible layers that are stacked together to form complex three-dimensional structures. This design provides greater design freedom and higher circuit density for high-end applications that require more signal layers or more complex layouts, such as aerospace, defense and medical imaging equipment.
The type of Rigid-Flex PCB depends on the specific application needs and design requirements. Choosing the right type can improve your board’s performance, reliability and productivity. When designing Rigid-Flex PCB, factors such as circuit layout, material selection, bending radius, etc. need to be considered to ensure that the final product meets the expected functional and performance requirements.
In summary, the diverse types and designs of Rigid-Flex PCB make it an indispensable key technology in the electronics industry, providing innovations and solutions for various applications.
The advantages of Rigid-Flex PCB
When talking about the advantages of Rigid-Flex PCBs, we first have to note how unique they are compared to traditional rigid circuit boards. These advantages include not only improved performance, but also increased design flexibility and reliability.
First of all, Rigid-Flex PCB has significant advantages in space utilization. Since they combine rigid and flexible parts, space inside the device can be used more efficiently. This combination allows the circuit board to better fit the form and structure of the device, saving valuable space in the design. Especially in the application of miniaturized equipment and high-density wiring, Rigid-Flex PCB can exert its unique advantages, making the overall equipment more compact and more powerful.
Secondly, Rigid-Flex PCB can also significantly reduce connection points. Traditional rigid circuit boards usually require connectors or cables to connect various parts, which not only increases the complexity of the system, but may also lead to unstable or failed connections. Rigid-Flex PCB can reduce the number of connection points by directly integrating rigid and flexible parts, thereby reducing the failure rate of the system and improving overall reliability.
In addition, the structural design of Rigid-Flex PCB also makes it more durable. Compared with traditional rigid circuit boards, the flexible part of Rigid-Flex PCB can better withstand external stresses such as vibration, impact and bending, thereby reducing the risk of damage caused by changes in the external environment. This improvement in durability not only extends the service life of the device, but also reduces the cost of maintenance and replacement, giving users a better experience.
To sum up, Rigid-Flex PCB has obvious advantages in saving space, improving reliability and durability. Their unique structural design makes them an indispensable key component in many modern electronic devices, providing strong support for innovation and development in all walks of life.
How to Design a Rigid-Flex PCB?
Designing a Rigid-Flex PCB is a comprehensive task that requires planning based on multiple factors. First, material selection is crucial. For rigid parts, commonly used materials include FR4 fiberglass reinforced panels, while for flexible parts, polyimide (PI) is a common choice due to its excellent flexibility and high temperature resistance. Material selection not only affects the performance of the board, but also directly affects manufacturing cost and reliability.
Secondly, the stack-up structure is a key consideration in the design. In a stack-up design, the number of rigid and flexible layers and the stacking sequence between them need to be determined. This involves a thorough evaluation of the board’s functionality and space constraints. For example, in mobile devices, space may be very limited, so the number of layers needs to be reduced to the minimum possible while still meeting the functional needs of the board.
Another important design consideration is the bend radius. Because the flex section needs to maintain the integrity of the circuit path when bending, the bend radius must be carefully considered. A radius that is too small may cause damage or breakage to the board, while a radius that is too large may result in unstable folding of the board. Therefore, the need for flexing and the reliability of the board must be balanced in the design.
In the design process, key steps include requirements analysis, schematic design, layout design, wiring design and final verification. During the requirements analysis phase, the board’s functionality, performance, and constraints need to be clearly defined. The principle design stage involves the drawing of circuit diagrams and the division of functional modules. During the layout design and wiring design stages, components need to be placed in appropriate locations and a wiring scheme designed to meet signal integrity and electromagnetic compatibility requirements. The final validation phase includes prototyping and functional testing to ensure the design meets expected performance metrics.
In short, designing Rigid-Flex PCB is a comprehensive engineering task that requires comprehensive consideration of materials, stacked structures, bending radius and other factors. Only with a thorough understanding of the board’s functional requirements and manufacturing constraints can a board be designed to meet performance and reliability requirements.
Why use ceramic Rigid-Flex PCB over other boards?
When considering circuit board selection, ceramic Rigid-Flex PCB is often a high-profile option. Compared with other materials, ceramic Rigid-Flex PCB has unique advantages in temperature stability, mechanical strength and electrical performance, making it stand out in specific application fields.
First, ceramic materials are known for their excellent temperature stability. In high-temperature environments, traditional circuit board materials may lose their stability, resulting in reduced circuit performance or even damage. However, ceramic Rigid-Flex PCB is able to maintain stability under extreme temperature conditions and is not affected by temperature fluctuations, ensuring the reliability and durability of the circuit system.
Secondly, ceramic Rigid-Flex PCB has excellent mechanical strength. The ceramic material itself has a high degree of hardness and pressure resistance, allowing the circuit board to remain stable when subjected to physical stress or vibration. This mechanical strength makes ceramic Rigid-Flex PCB particularly suitable for applications that require long-term stable operation, such as the aerospace field or industrial automation equipment.
Finally, ceramic Rigid-Flex PCBs also excel in electrical performance. Ceramic materials have excellent insulation properties and dielectric properties, which can effectively reduce energy loss and interference during signal transmission. This makes ceramic Rigid-Flex PCBs excellent in applications with high frequencies and high-speed transmission, such as communications equipment and radar systems.
Overall, ceramic Rigid-Flex PCB has obvious advantages in applications in high-temperature environments or extreme conditions. Its excellent temperature stability, mechanical strength and electrical performance make it the first choice in many industries. As technology continues to develop, ceramic Rigid-Flex PCB will continue to play an important role and enable innovation and applications in more fields.
What is the Rigid-Flex PCB Fabrication Process?
When we talk about the manufacturing process of Rigid-Flex PCB, we enter a complex and sophisticated area. This advanced circuit board technology requires multiple processes, each of which must be precisely controlled to ensure the quality and performance of the final product. Below we will delve into the manufacturing process of Rigid-Flex PCB:
The first is lamination. This is the first and one of the most critical steps in the Rigid-Flex PCB manufacturing process. During the lamination process, rigid and flexible materials are combined into one body to create the desired laminate structure. This requires precisely controlled temperature and pressure to ensure perfect bonding between the individual layers, as well as the required thickness and strength.
Next comes drilling. In this step, manufacturers use advanced drilling equipment to accurately drill holes in the board as per the design requirements. These holes will be used to mount components and connect wires between different layers. The accuracy of drilling is critical to the success of subsequent steps.
Copper plating is the next critical step. In this process, a layer of copper is chemically deposited on the board. This step is to ensure good conductivity and connectivity while also ensuring protection of the flexible parts. The uniformity and thickness of copper plating are key factors in ensuring the stability of circuit board performance.
Finally comes the cutting. In this step, manufacturers use high-precision cutting equipment to cut the circuit board into the required shape and size according to the design requirements. This includes tailoring rigid and flexible sections to ensure they meet design specifications and are suitable for the specific application environment.
Overall, the manufacturing process of Rigid-Flex PCB is a complex process that requires a high degree of technology and precise control. Each step must be performed with precision to ensure the quality and reliability of the final product. Only in this way can high-quality Rigid-Flex PCBs suitable for various high-end applications be produced.
The application of ceramic Rigid-Flex PCB
Ceramic Rigid-Flex PCB, as a circuit board with a special combination of materials, plays a vital role in medical equipment, aerospace, military and other fields. Its unique properties make it ideal in these areas.
First of all, the medical equipment industry has extremely high requirements for the stability and reliability of circuit boards. Ceramic Rigid-Flex PCB can perform well in various harsh medical environments, such as medical imaging equipment, implantable medical devices, etc. Its high temperature stability and corrosion resistance enable it to operate stably for a long time in the body or in external equipment, ensuring the reliability and safety of medical equipment.
Secondly, in the aerospace field, ceramic Rigid-Flex PCB also plays an important role. Aerospace equipment has extremely high requirements for lightweight, high temperature resistance and reliability of electronic equipment, and ceramic Rigid-Flex PCB is an ideal choice to meet these requirements. Its lightweight design can reduce the overall weight of the aircraft, while its high-temperature stability ensures the normal operation of electronic equipment in extreme space environments.
In addition, the military field is also one of the important application fields of ceramic Rigid-Flex PCB. Military equipment often needs to be used for combat or reconnaissance in harsh environmental conditions, so the stability and reliability of circuit boards are extremely high. The high temperature resistance, impact resistance and corrosion resistance of ceramic Rigid-Flex PCB enable it to operate stably in extreme battlefield environments, ensuring the combat effectiveness of military equipment and the safety of soldiers.
To sum up, the wide application of ceramic Rigid-Flex PCB in medical equipment, aerospace, military and other fields demonstrates its unique advantages and value. With the continuous development and innovation of technology, I believe it will have wider application prospects in more fields.
FAQs
How is Rigid-Flex PCB different from traditional rigid circuit boards?
Rigid-Flex PCB offers greater flexibility and reliability than traditional rigid circuit boards. They can be designed to better accommodate space constraints and reduce connection points, resulting in increased reliability and lower failure rates. Additionally, Rigid-Flex PCBs can reduce assembly time and costs because they reduce the number of connectors and cables required.
What are the key factors to consider in the design of Rigid-Flex PCB?
There are many factors to consider when designing Rigid-Flex PCB, including material selection, stack-up structure, bending radius, wiring paths, etc. The bending radius is a particularly important factor, which directly affects the reliability and life of the flexible part. In addition, the wiring path needs to avoid pressure and tension as much as possible to ensure the stability of the flexible part.
What is the manufacturing process of Rigid-Flex PCB?
The manufacturing process of Rigid-Flex PCB includes several main steps: lamination, drilling, copper plating, cutting, etc. During the lamination process, the rigid and flexible parts are brought together and cured using heat pressing technology. Next, drilling and copper plating are required to make the circuit connections. Finally, the circuit board is segmented into its final shape through a precision cutting process.
In what fields are ceramic Rigid-Flex PCBs widely used?
Ceramic Rigid-Flex PCB is widely used in medical equipment, aerospace, military and other fields due to its high temperature stability and excellent electrical properties. For example, in medical equipment, ceramic Rigid-Flex PCBs can be used in control and sensor systems in high-temperature sterilization environments.