What is Panasonic Megtron 7 PCB?
Panasonic Megtron 7 PCB Manufacturer.Panasonic Megtron 7 PCB Manufacturer specializes in producing high-performance printed circuit boards (PCBs) using Megtron 7 material. Renowned for its superior electrical and thermal properties, Megtron 7 ensures exceptional signal integrity and reliability in demanding applications. This advanced PCB material is ideal for high-speed and high-frequency electronics, making it a preferred choice for industries such as telecommunications, aerospace, and automotive. The manufacturer’s expertise in utilizing Megtron 7 material ensures the production of high-quality, durable, and efficient PCBs that meet the rigorous standards of modern electronic devices.
Panasonic Megtron 7 PCB is a high-performance printed circuit board material developed by Panasonic, designed specifically for high-speed and high-frequency applications. It is part of the Megtron series, which is known for its superior electrical properties, thermal stability, and reliability. Megtron 7 is particularly notable for its low dielectric constant (Dk) and low dissipation factor (Df), making it ideal for use in advanced telecommunications, data centers, and other high-speed digital applications.
The dielectric constant (Dk) of Megtron 7 is approximately 3.3, and its dissipation factor (Df) is around 0.002. These properties ensure minimal signal loss and distortion, maintaining signal integrity even at very high frequencies. Additionally, Megtron 7 offers excellent thermal performance with a high glass transition temperature (Tg) of 210°C, making it suitable for applications that require reliable performance under high thermal stress.
The Types of Panasonic Megtron 7 PCB
Panasonic Megtron 7 PCB materials come in various types and configurations to meet different application requirements. These include:
Single-Layer Megtron 7 PCBs: Ideal for straightforward high-frequency circuits such as antennas and RF amplifiers. These boards offer simplicity and cost-effectiveness while providing excellent performance for specific applications.
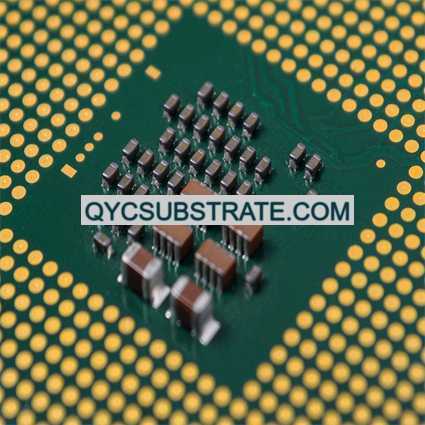
Panasonic Megtron 7 PCB Manufacturer
Multilayer Megtron 7 PCBs: Used in complex systems where multiple high-frequency circuits need to be integrated into a compact space. Multilayer boards enhance functionality and performance, making them suitable for high-speed networking devices and telecommunication systems.
Hybrid Megtron 7 PCBs: Combine Megtron 7 materials with other types of laminates to achieve specific performance characteristics. This allows designers to optimize different sections of the PCB for high-frequency performance and cost efficiency.
Flexible Megtron 7 PCBs: Provide flexibility in design and are used in applications where the PCB needs to be bent or folded, such as in aerospace and medical devices. They offer reliability and high performance in dynamic environments.
The Advantages of Panasonic Megtron 7 PCB
Panasonic Megtron 7 PCB offers several significant advantages for high-speed and high-frequency applications:
Low Dielectric Constant and Dissipation Factor: The low Dk and Df values of Megtron 7 ensure minimal signal loss and distortion, maintaining high signal integrity even at very high frequencies.
High Thermal Stability: With a high Tg of 210°C, Megtron 7 materials provide excellent thermal performance, making them suitable for applications that experience significant thermal stress.
Superior Reliability: Megtron 7 PCBs offer robust mechanical properties and chemical resistance, ensuring long-term reliability and durability in harsh operating environments.
Compatibility with High-Density Interconnects: Megtron 7 materials support the fabrication of high-density interconnects (HDI), enabling more compact and complex PCB designs for advanced electronic devices.
Improved Signal Integrity: The materials used in Megtron 7 PCBs are optimized for high-speed signal transmission, reducing signal attenuation and crosstalk, which is critical for high-performance applications.
How to Design a Panasonic Megtron 7 PCB?
Designing a Panasonic Megtron 7 PCB involves several key steps and considerations to ensure optimal performance:
Choose the appropriate thickness and dielectric properties of Megtron 7 materials based on the specific application requirements. This selection is critical as it directly impacts the circuit’s performance and stability.
Precisely control the impedance of transmission lines to ensure signal integrity. Use electromagnetic simulation software to model and verify the impedance of the PCB traces.
Minimize the length of high-frequency signal paths to reduce signal loss and interference. Employ differential pair routing for high-speed differential signals to minimize crosstalk and electromagnetic interference.
Design robust grounding and power distribution networks to ensure stable operation and minimize noise. Utilize ground planes to provide a low-impedance path for return currents.
Incorporate effective thermal management strategies, such as thermal vias and heatsinks, to dissipate heat generated by high-power components and maintain stable operation.
Ensure the PCB design is compatible with standard manufacturing processes. Work closely with the PCB manufacturer to confirm design parameters and fabrication capabilities.
Why Use Panasonic Megtron 7 PCB Over Other Boards?
Choosing Panasonic Megtron 7 PCB over other types of PCB materials offers several benefits, making it a preferred choice for specific applications:
The low dielectric constant and low dissipation factor of Megtron 7 materials make them excellent for high-frequency and high-speed digital applications, ensuring minimal signal loss and high signal fidelity.
Megtron 7 materials can withstand high temperatures without degrading, making them suitable for applications that experience significant thermal stress.
Megtron 7 PCBs offer superior mechanical strength and chemical resistance, ensuring long-term reliability and durability even in harsh environments.
Megtron 7 materials support various PCB configurations, including single-layer, multilayer, hybrid, and flexible designs, allowing for greater design flexibility and optimization.
As technology advances and the demand for higher data rates and frequencies increases, Megtron 7 PCBs provide a future-proof solution that can support emerging technologies and standards.
What is the Panasonic Megtron 7 PCB Fabrication Process?
The fabrication process of Panasonic Megtron 7 PCB involves several critical steps to ensure high performance and reliability:
Select and prepare the Megtron 7 laminate material according to design specifications. The material should be cut to the required dimensions and cleaned to remove contaminants.
For multilayer PCBs, laminate the individual layers together under high temperature and pressure. Ensure proper alignment and bonding of the layers.
Drill holes for vias and component leads according to the design layout. Precision drilling is essential to maintain the integrity of high-frequency signals.
Plate the drilled holes and vias with copper to create electrical connections between the layers. This step ensures reliable signal transmission and mechanical stability.
Use photolithography to transfer the circuit pattern onto the laminate material. This process involves coating the material with a photosensitive film, exposing it to UV light through a mask, and developing the pattern.
Etch away the unwanted copper to reveal the desired circuit pattern. This step requires precise control to ensure accurate and clean traces.
Apply a surface finish, such as ENIG (Electroless Nickel Immersion Gold) or HASL (Hot Air Solder Leveling), to protect the copper traces and ensure good solderability.
Perform electrical testing and visual inspection to verify the PCB’s performance and quality. This includes checking for impedance control, signal integrity, and overall functionality.
The Application of Panasonic Megtron 7 PCB
Panasonic Megtron 7 PCBs are used in various high-speed and high-frequency applications due to their superior performance and reliability:
Megtron 7 PCBs are extensively used in wireless communication systems, including mobile phones, base stations, and satellite communications. They enable high-speed data transmission and efficient signal processing.
In data centers, Megtron 7 PCBs are used in servers, routers, and switches to support high-speed data processing and transmission, ensuring reliable and efficient operation.
Megtron 7 PCBs are used in radar systems, satellite navigation, and communication devices in the aerospace industry. Their excellent thermal stability and reliability ensure optimal performance in extreme environments.
Megtron 7 PCBs are employed in military communication systems, radar, and electronic warfare equipment. Their robust construction and high performance make them suitable for mission-critical applications.
Megtron 7 PCBs are used in advanced driver-assistance systems (ADAS), radar sensors, and high-speed data communication in modern vehicles. They ensure reliable operation in harsh automotive environments.
FAQs
What are the main advantages of Panasonic Megtron 7 PCB?
The main advantages include low dielectric constant, low dissipation factor, high thermal stability, superior reliability, and compatibility with high-density interconnects.
What application areas are suitable for Panasonic Megtron 7 PCB?
Panasonic Megtron 7 PCBs are suitable for telecommunications, data centers, aerospace, military, and automotive applications, among others.
What is the difference between Panasonic Megtron 7 PCB and traditional FR-4 PCB?
Panasonic Megtron 7 PCB offers better signal performance, lower signal loss, and improved reliability in high-frequency and high-speed applications compared to traditional FR-4 PCB, which is typically used for lower frequency and less demanding applications.
What factors should be considered when designing a Panasonic Megtron 7 PCB?
Factors to consider include material selection, impedance control, signal path layout, grounding and power planes, thermal management, and manufacturability.