Multilayer Ceramic PCBs Manufacturer.Multilayer Ceramic PCBs manufacturers specialize in producing high-performance circuit boards that utilize ceramic as the substrate material. These PCBs offer superior thermal management, high-frequency performance, and exceptional reliability, making them ideal for aerospace, military, medical, and advanced electronic applications. The manufacturing process involves precise layering, sintering, and metalizing techniques to achieve optimal electrical properties and miniaturization. These manufacturers provide tailored solutions to meet specific industry requirements, ensuring robust performance in challenging environments.
What is a Multilayer Ceramic PCB?
Multilayer Ceramic PCBs are advanced circuit boards that consist of multiple layers of ceramic material, each layer featuring its own circuitry. These layers are laminated together to form a single, compact board that offers enhanced electrical performance and reliability. The use of ceramic as a substrate material in multilayer PCBs provides superior thermal management, mechanical strength, and electrical insulation compared to traditional PCB materials like FR4 or metal cores.
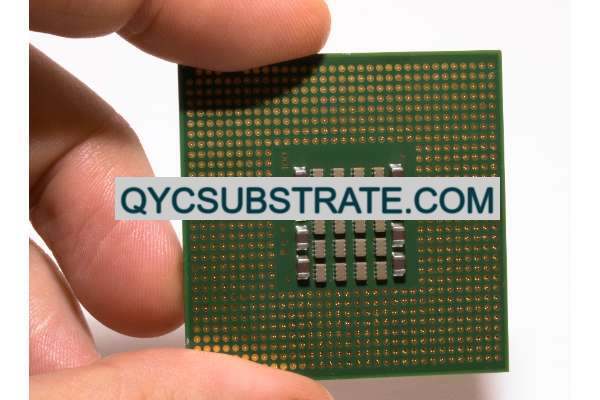
Multilayer Ceramic PCBs Manufacturer
The multilayer structure allows for more complex circuit designs, as each layer can house distinct circuit paths, enabling the creation of highly integrated and compact electronic systems. This structure is particularly advantageous in applications where space is limited but the need for advanced functionality is high. Multilayer ceramic PCBs are commonly used in industries such as aerospace, medical devices, telecommunications, and high-frequency electronics, where performance and durability are critical.
The Types of Multilayer Ceramic PCBs
Multilayer Ceramic PCBs can be categorized based on the number of layers, the type of ceramic material used, and the specific application needs.
In terms of the number of layers, Multilayer Ceramic PCBs can range from two-layer designs to boards with ten or more layers. Each additional layer allows for more complex circuitry and integration of components, which is essential in high-density applications like microelectronics and RF circuits.
The choice of ceramic material also differentiates types of Multilayer Ceramic PCBs. Common materials include alumina (Al₂O₃), aluminum nitride (AlN), and beryllium oxide (BeO). Alumina is widely used due to its excellent electrical insulation and thermal properties. Aluminum nitride is preferred for applications requiring superior thermal conductivity, while beryllium oxide offers the highest thermal conductivity among ceramic materials, making it ideal for very high-power applications.
Application-specific types of Multilayer Ceramic PCBs are also available. For example, high-frequency multilayer ceramic PCBs are designed for RF and microwave applications, where signal integrity and low loss are critical. High-power multilayer ceramic PCBs are tailored for power electronics, where efficient heat dissipation is necessary to maintain performance and reliability.
The Advantages of Multilayer Ceramic PCBs
Multilayer Ceramic PCBs offer numerous advantages, making them a preferred choice for complex and high-performance electronic applications. One of the primary benefits is their superior thermal management capabilities. Ceramic materials like alumina and aluminum nitride have high thermal conductivity, which allows them to dissipate heat more effectively than traditional PCB materials. This is crucial in applications where overheating can lead to failure or degraded performance.
Another significant advantage is the high electrical insulation provided by ceramic substrates. This property ensures that the circuits within each layer are well isolated, preventing interference and cross-talk, which is essential in high-frequency and high-density applications. The mechanical strength of ceramic also contributes to the durability and longevity of Multilayer Ceramic PCBs, making them suitable for use in harsh environments.
The multilayer structure allows for the integration of more complex circuits in a smaller footprint. This is particularly beneficial in applications such as mobile devices, aerospace systems, and medical implants, where space is at a premium. Additionally, the ability to design boards with multiple layers enhances design flexibility, enabling engineers to create more sophisticated and efficient electronic systems.
Lastly, the reliability of Multilayer Ceramic PCBs is another key advantage. Ceramic materials are resistant to moisture, chemicals, and extreme temperatures, making these PCBs highly durable and capable of maintaining performance over long periods and under challenging conditions.
How to Design a Multilayer Ceramic PCB
Designing a Multilayer Ceramic PCB involves several critical steps to ensure that the final product meets the required specifications for performance, reliability, and manufacturability. The process begins with defining the application requirements, including electrical, thermal, and mechanical considerations. This involves determining the number of layers needed, the choice of ceramic material, and the layout of the circuitry.
Once the requirements are established, a detailed schematic of the circuit is created. This schematic serves as the blueprint for the PCB layout, which involves placing components and routing traces on each layer. The multilayer nature of the board allows for complex routing, with signal layers typically separated by ground or power planes to reduce noise and interference.
Thermal management is a crucial aspect of the design process, given the high thermal conductivity of ceramic materials. Engineers must consider the placement of heat-generating components and design the board to maximize heat dissipation. This may involve incorporating thermal vias or heatsinks into the design.
Another important consideration in the design of Multilayer Ceramic PCBs is the manufacturing process. The design must be compatible with the capabilities of the chosen fabrication process, which involves careful attention to the thickness of the layers, the alignment of vias, and the material properties. The final step is to simulate the performance of the design using specialized software to ensure that it meets all electrical and thermal requirements.
Why Use Multilayer Ceramic PCBs Over Other Boards?
Multilayer Ceramic PCBs offer several advantages over other types of PCBs, particularly in applications where performance, reliability, and compactness are critical. The primary reason for choosing a multilayer ceramic board is its superior thermal management capabilities. Ceramic materials like alumina and aluminum nitride can dissipate heat much more effectively than traditional PCB materials, making them ideal for high-power and high-frequency applications.
The electrical insulation provided by ceramic materials is another key benefit. This insulation ensures that the circuits within each layer remain isolated from one another, reducing the risk of interference and improving overall signal integrity. This makes Multilayer Ceramic PCBs particularly suitable for RF and microwave applications, where maintaining signal quality is essential.
The compact nature of Multilayer Ceramic PCBs is another reason for their use in space-constrained applications. By stacking multiple layers of circuitry, these boards can integrate more functionality into a smaller footprint, making them ideal for use in mobile devices, aerospace systems, and medical implants.
Finally, the reliability and durability of ceramic materials make Multilayer Ceramic PCBs a preferred choice for applications in harsh environments. Ceramic substrates are resistant to moisture, chemicals, and extreme temperatures, ensuring that the board can maintain its performance over time, even in challenging conditions.
What is the Multilayer Ceramic PCB Fabrication Process?
The fabrication of Multilayer Ceramic PCBs is a complex process that involves multiple steps to ensure that each layer of the board is accurately produced and aligned. The process begins with the preparation of the ceramic substrate, which is typically made from materials like alumina or aluminum nitride. The substrate is processed into thin layers, each of which will form a layer of the final PCB.
Conductive traces are then applied to each layer using techniques such as screen printing or thin-film deposition. These traces form the circuitry for each layer of the PCB. Vias are also created to connect the different layers electrically. These vias are typically filled with conductive material, such as silver or copper, to ensure good electrical connectivity between layers.
Once the individual layers are prepared, they are laminated together under heat and pressure to form a single, cohesive board. This lamination process requires precise alignment to ensure that the vias and traces are properly connected across all layers. The laminated board is then subjected to additional processing, such as sintering, to fuse the ceramic layers together and enhance the mechanical strength of the board.
After lamination and sintering, the Multilayer Ceramic PCB undergoes surface finishing, which may include the application of protective coatings or the addition of surface mount pads. The final steps in the fabrication process involve the assembly of components onto the board and rigorous testing to ensure that the PCB meets all required electrical, thermal, and mechanical specifications.
The Application of Multilayer Ceramic PCBs
Multilayer Ceramic PCBs are used in a wide range of applications where performance, reliability, and compactness are critical. In the aerospace industry, these PCBs are used in avionics, navigation systems, and communication equipment, where they provide the necessary thermal management and reliability in extreme conditions.
In the medical field, Multilayer Ceramic PCBs are found in devices such as pacemakers, defibrillators, and imaging equipment. Their compact size and ability to integrate complex circuitry make them ideal for implantable devices and other advanced medical technologies.
Telecommunications is another sector that benefits from Multilayer Ceramic PCBs, particularly in high-frequency applications such as base stations, satellite communications, and radar systems. The excellent electrical performance and signal integrity of these PCBs are crucial for maintaining communication quality.
In consumer electronics, Multilayer Ceramic PCBs are used in products such as smartphones, tablets, and wearable devices, where space constraints and high performance are key considerations. The ability to stack multiple layers of circuitry in a compact form factor makes these PCBs well-suited for modern electronic devices.
High-power electronics, such as power amplifiers and power supplies, also utilize Multilayer Ceramic PCBs due to their superior thermal management capabilities. These PCBs help dissipate heat effectively, ensuring that the electronic components operate efficiently and reliably over time.
FAQs
What are Multilayer Ceramic PCBs?
Multilayer Ceramic PCBs are circuit boards that consist of multiple layers of ceramic material, each with its own circuitry, laminated together to form a single board.
What types of Multilayer Ceramic PCBs are available?
Types include variations based on the number of layers, the type of ceramic material used, and application-specific designs, such as those for high-frequency or high-power applications.
What are the advantages of Multilayer Ceramic PCBs?
Advantages include superior thermal management, high electrical insulation, mechanical strength, compact design, and high reliability.
How is a Multilayer Ceramic PCB designed?
Design involves defining application requirements, creating circuit schematics, optimizing the layout for multilayer routing, considering thermal management, and ensuring manufacturability.
What is the fabrication process for Multilayer Ceramic PCBs?
The process includes preparing the ceramic substrate, applying conductive traces, laminating layers together, sintering, surface finishing, and assembling components.