What is LTCC (Low-Temperature Co-fired Ceramic) PCBs?
LTCC (Low-Temperature Co-fired Ceramic) PCBs Manufacturer.LTCC (Low-Temperature Co-fired Ceramic) PCB manufacturers specialize in producing advanced circuit boards that integrate multiple layers of ceramic and conductive materials. These PCBs offer superior performance in high-frequency and high-temperature environments, making them ideal for aerospace, telecommunications, and medical applications. LTCC technology allows for compact, reliable, and highly efficient designs, meeting the demands of modern electronic devices.
LTCC (Low-Temperature Co-fired Ceramic) PCBs are a type of advanced ceramic circuit board that is manufactured through a unique process where ceramic materials and conductive elements are co-fired at relatively low temperatures (typically around 850°C). This process allows for the creation of a multilayer ceramic substrate that can integrate both passive components and complex circuitry within a compact and robust structure. LTCC PCBs are known for their superior mechanical strength, thermal stability, and excellent electrical properties, which make them particularly well-suited for high-frequency and high-power applications.
The technology behind LTCC PCBs dates back to the development of co-fired ceramic processes, where layers of ceramic materials, such as alumina or glass-ceramic composites, are laminated together and fired in a kiln. What distinguishes LTCC from other types of ceramic substrates is the ability to incorporate multiple layers of circuits and components, including resistors, capacitors, and inductors, into a single monolithic structure. This integration allows for a significant reduction in the size of the electronic assembly, making LTCC PCBs highly desirable in applications where space and weight are critical constraints, such as in aerospace, automotive, and telecommunication industries.
Moreover, LTCC PCBs offer outstanding electrical insulation properties, which is essential for preventing signal loss and interference in high-frequency circuits. The low dielectric constant and loss tangent of the ceramic materials used in LTCC substrates ensure that the integrity of signals is maintained, even at frequencies exceeding several GHz. This makes LTCC PCBs particularly suitable for radio frequency (RF) and microwave applications, where signal integrity is paramount.
Additionally, LTCC PCBs are highly resistant to thermal expansion and contraction, which makes them ideal for use in harsh environments where temperature fluctuations are common. The thermal stability of LTCC PCBs ensures that they maintain their structural and electrical integrity even under extreme temperature conditions, which is a critical requirement in aerospace and automotive applications. Furthermore, the co-firing process allows for the integration of materials with different thermal expansion coefficients, which can be used to create tailored thermal management solutions for high-power devices.
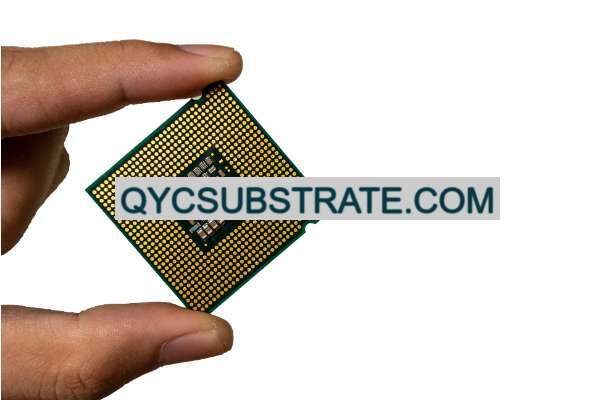
LTCC (Low-Temperature Co-fired Ceramic) PCBs Manufacturer
In summary, LTCC PCBs are an advanced type of ceramic circuit board that offers a unique combination of mechanical strength, thermal stability, and excellent electrical properties. Their ability to integrate multiple layers of circuitry and components into a single compact structure makes them ideal for a wide range of high-performance applications, particularly in industries where size, weight, and reliability are critical factors.
The Types of LTCC PCBs
LTCC (Low-Temperature Co-fired Ceramic) PCBs come in various types, each designed to meet specific application requirements. The primary types of LTCC PCBs include single-layer and multilayer LTCC substrates, with the latter being the most common due to its ability to integrate complex circuitry within a compact form factor.
Single-layer LTCC PCBs are the simplest form of LTCC technology. These PCBs consist of a single layer of ceramic material that acts as the substrate, onto which conductive traces and passive components are embedded. Single-layer LTCC PCBs are typically used in applications where the circuit design is relatively simple and does not require the integration of multiple components or complex routing. Despite their simplicity, single-layer LTCC PCBs still offer the inherent advantages of ceramic materials, such as excellent thermal and mechanical properties, making them suitable for certain high-reliability applications.
Multilayer LTCC PCBs are the most widely used type of LTCC PCBs. These PCBs are composed of multiple layers of ceramic and conductive materials that are laminated together and co-fired in a single step. The multilayer structure allows for the integration of more complex circuitry, including embedded passive components like resistors, capacitors, and inductors, which can be incorporated within the layers of the substrate. This ability to embed components within the PCB itself leads to significant space savings and improved performance, as it reduces parasitic effects and shortens signal paths.
Multilayer LTCC PCBs are particularly beneficial in applications where high-density interconnections and miniaturization are required. The multiple layers enable designers to create intricate circuit designs with a high degree of flexibility in routing and component placement. Moreover, the multilayer structure can support the implementation of sophisticated electrical functions, such as signal filtering, impedance matching, and noise suppression, which are critical in RF and microwave applications.
In addition to standard multilayer LTCC PCBs, there are also variations designed to meet specific needs. For example, some LTCC PCBs are designed with embedded cavities that can house additional components or provide pathways for fluids or gases in microfluidic applications. Others may incorporate through-hole vias or blind vias to facilitate interconnections between different layers or to connect external components to the internal circuitry.
Furthermore, LTCC technology can be customized to meet the thermal management needs of high-power applications. By integrating thermal vias or heat sinks into the LTCC substrate, designers can effectively dissipate heat generated by power-intensive components, ensuring reliable operation under demanding conditions.
In conclusion, the types of LTCC PCBs range from simple single-layer substrates to complex multilayer structures, each offering unique advantages depending on the application. The ability to tailor the design of LTCC PCBs to meet specific electrical, mechanical, and thermal requirements makes them a versatile solution for a wide range of high-performance applications.
The Advantages of LTCC PCBs
LTCC (Low-Temperature Co-fired Ceramic) PCBs offer a host of advantages that make them highly suitable for demanding applications across various industries. One of the primary benefits of LTCC PCBs is their exceptional thermal performance. The ceramic materials used in LTCC PCBs have excellent thermal conductivity, which helps to dissipate heat effectively. This is particularly important in high-power electronic devices, where excessive heat generation can lead to component failure. The ability of LTCC PCBs to manage heat efficiently makes them ideal for applications such as power amplifiers, LED modules, and automotive electronics.
Another significant advantage of LTCC PCBs is their superior electrical properties. The ceramic substrate used in LTCC technology exhibits a low dielectric constant and low loss tangent, which are critical for high-frequency applications. These properties ensure minimal signal loss and high signal integrity, making LTCC PCBs ideal for RF and microwave circuits. In addition, the low dielectric constant allows for reduced signal propagation delays, which is essential in high-speed digital applications.
LTCC PCBs also excel in mechanical durability and reliability. The ceramic material is inherently rigid and robust, providing excellent resistance to mechanical stress, vibrations, and shocks. This makes LTCC PCBs suitable for use in harsh environments, such as aerospace and defense applications, where electronic components are exposed to extreme conditions. Furthermore, LTCC PCBs are resistant to thermal expansion, which helps maintain the integrity of the circuit under varying temperatures, ensuring consistent performance over time.
The ability to integrate passive components directly into the LTCC substrate is another notable advantage. By embedding resistors, capacitors, and inductors within the ceramic layers, designers can reduce the overall size and weight of the electronic assembly. This miniaturization is particularly valuable in applications where space is at a premium, such as in mobile devices and wearable technology. Additionally, the integration of passive components helps to improve circuit performance by minimizing parasitic effects and reducing the number of interconnections, which can introduce noise and signal degradation.
LTCC PCBs are also highly customizable, allowing for the creation of complex, multilayered circuits that meet specific design requirements. The flexibility in design, combined with the ability to incorporate various materials and components within the substrate, makes LTCC PCBs an ideal solution for complex, high-performance electronic systems. Moreover, the co-firing process used in LTCC manufacturing allows for the production of high-precision circuits with tight tolerances, ensuring consistent quality and performance.
In summary, LTCC PCBs offer numerous advantages, including excellent thermal performance, superior electrical properties, mechanical durability, and the ability to integrate passive components. These benefits make LTCC PCBs a preferred choice for a wide range of high-performance applications, particularly in industries where reliability, miniaturization, and high-frequency operation are critical.
How to Design an LTCC PCB?
Designing an LTCC (Low-Temperature Co-fired Ceramic) PCB involves several steps that require careful consideration of the electrical, mechanical, and thermal requirements of the application. The design process begins with defining the circuit requirements and creating a schematic that outlines the components and their connections. Once the schematic is complete, the next step is to translate it into a layout that can be used to fabricate the LTCC PCB.
One of the first considerations in LTCC PCB design is the selection of materials. The choice of ceramic material, such as alumina or glass-ceramic composites, will depend on the specific requirements of the application, including the operating frequency, thermal conductivity, and mechanical strength. Additionally, the type of conductive materials used for the traces and vias must be chosen based on their compatibility with the ceramic substrate and the firing process. Common choices include silver, gold, and platinum, which offer excellent electrical conductivity and stability at high temperatures.
The next step in the design process is to create a layout that optimizes the placement of components and routing of traces. In LTCC PCBs, it is crucial to minimize signal path lengths to reduce parasitic inductance and capacitance, which can degrade the performance of high-frequency circuits. The layout should also ensure proper spacing between traces and components to prevent crosstalk and signal interference. In multilayer LTCC PCBs, careful attention must be paid to the placement of vias and the distribution of ground and power planes to maintain signal integrity and reduce electromagnetic interference (EMI).
Thermal management is another critical aspect of LTCC PCB design. The high thermal conductivity of the ceramic substrate can be leveraged to dissipate heat away from power-intensive components. Designers can incorporate thermal vias, heat sinks, or embedded cooling structures within the LTCC substrate to enhance heat
dissipation. Proper thermal design ensures that the LTCC PCB can operate reliably under high-power conditions without overheating or thermal degradation.
The co-firing process used in LTCC manufacturing allows for the integration of passive components directly into the ceramic substrate. This capability should be considered during the design phase, as it can significantly reduce the overall size and complexity of the PCB. Designers can embed resistors, capacitors, and inductors within the ceramic layers, eliminating the need for discrete components and reducing the number of solder joints, which improves reliability.
Once the layout is complete, the design is typically converted into a Gerber file, a standard format used in the PCB fabrication industry. The Gerber file contains all the necessary information for the manufacturer to produce the LTCC PCB, including the layer structure, trace routing, via placement, and component positions.
In conclusion, designing an LTCC PCB involves careful consideration of material selection, component placement, trace routing, thermal management, and the integration of passive components. By optimizing these factors, designers can create high-performance LTCC PCBs that meet the demanding requirements of modern electronic systems.
Why Use Ceramic LTCC PCBs Over Other Boards?
Ceramic LTCC (Low-Temperature Co-fired Ceramic) PCBs offer several distinct advantages over traditional PCB materials, such as FR4, which make them an attractive choice for specific applications. One of the primary reasons for choosing ceramic LTCC PCBs is their superior thermal performance. The ceramic materials used in LTCC PCBs have excellent thermal conductivity, which allows for efficient heat dissipation. This is particularly important in high-power applications, such as RF amplifiers and LED lighting, where excessive heat generation can lead to component failure and reduced reliability.
In contrast, traditional PCB materials like FR4 have relatively poor thermal conductivity, which can result in localized hotspots and thermal stress on components. This limitation makes FR4 less suitable for applications that require efficient thermal management. LTCC PCBs, with their ability to integrate thermal vias and heat sinks directly into the substrate, provide a more effective solution for managing heat and ensuring the longevity and reliability of electronic devices.
Another significant advantage of ceramic LTCC PCBs is their superior electrical properties, particularly in high-frequency applications. The low dielectric constant and low loss tangent of the ceramic materials used in LTCC substrates ensure minimal signal loss and high signal integrity. This makes LTCC PCBs ideal for RF and microwave circuits, where maintaining signal fidelity is critical. In contrast, traditional PCB materials like FR4 have higher dielectric losses, which can degrade signal quality at high frequencies, making them less suitable for advanced communication systems and radar applications.
Ceramic LTCC PCBs also offer enhanced mechanical durability and reliability compared to traditional PCB materials. The ceramic substrate is inherently rigid and robust, providing excellent resistance to mechanical stress, vibrations, and shocks. This makes LTCC PCBs particularly well-suited for use in harsh environments, such as aerospace, automotive, and defense applications, where electronic components are subjected to extreme conditions. Additionally, LTCC PCBs are resistant to thermal expansion, which helps maintain the integrity of the circuit under varying temperatures, ensuring consistent performance over time.
The ability to integrate passive components directly into the LTCC substrate is another advantage that sets ceramic PCBs apart from traditional boards. By embedding resistors, capacitors, and inductors within the ceramic layers, designers can reduce the overall size and weight of the electronic assembly, which is particularly valuable in applications where space is at a premium. This level of integration is challenging to achieve with traditional PCB materials, which typically require the use of discrete components mounted on the surface of the board.
Furthermore, the co-firing process used in LTCC PCB manufacturing allows for the production of high-precision circuits with tight tolerances, ensuring consistent quality and performance. This is particularly important in applications where reliability and repeatability are critical, such as in medical devices, sensors, and communication equipment.
In summary, ceramic LTCC PCBs offer numerous advantages over traditional PCB materials, including superior thermal performance, excellent electrical properties, enhanced mechanical durability, and the ability to integrate passive components. These benefits make LTCC PCBs the preferred choice for high-performance applications in industries where reliability, miniaturization, and high-frequency operation are critical.
What is the LTCC PCB Fabrication Process?
The fabrication process of LTCC (Low-Temperature Co-fired Ceramic) PCBs involves several steps that combine advanced ceramic and metallization technologies to create a robust and high-performance circuit board. The process begins with the preparation of ceramic tapes, which serve as the substrate material. These tapes are typically made from a ceramic powder, such as alumina or a glass-ceramic composite, mixed with organic binders and solvents to create a flexible and manageable sheet.
Once the ceramic tapes are prepared, the next step is to print the conductive patterns onto the tapes. This is typically done using screen printing, a process where a conductive paste, often composed of metals like silver, gold, or platinum, is applied through a stencil onto the ceramic tape. The paste forms the electrical traces, pads, and other conductive elements of the circuit. If the design requires multiple layers, the process is repeated for each layer, with vias being created to connect the different layers electrically. Vias are typically formed by punching holes through the ceramic tapes and filling them with conductive paste.
After the conductive patterns are printed, the individual layers of the LTCC PCB are laminated together. This involves stacking the ceramic tapes in the correct order and applying pressure and heat to bond the layers into a single cohesive unit. The laminated stack is then subjected to a co-firing process, where it is heated in a kiln at temperatures around 850°C. During this firing process, the organic binders in the ceramic tapes burn off, and the ceramic particles fuse together to form a solid, rigid substrate. Simultaneously, the conductive paste sinters, creating a continuous and durable conductive network.
One of the key advantages of the LTCC PCB fabrication process is the ability to integrate passive components, such as resistors, capacitors, and inductors, directly into the ceramic substrate. This is achieved by incorporating resistive or dielectric materials into the conductive paste or by using specially formulated layers within the ceramic stack. These embedded components offer significant space savings and improve the overall performance and reliability of the circuit by reducing the number of interconnections and minimizing parasitic effects.
Once the LTCC PCB is co-fired, the next step is to apply any necessary surface finishes, such as gold plating, to protect the conductive traces and improve solderability. Additional processing steps, such as laser trimming, may also be performed to fine-tune the electrical characteristics of the embedded components or to create precision features in the circuit.
Finally, the LTCC PCB undergoes a series of inspections and tests to ensure that it meets the required specifications. These tests may include electrical testing, dimensional inspection, and environmental testing to verify the board’s performance and reliability under various conditions.
In conclusion, the fabrication process of LTCC PCBs is a complex and highly specialized procedure that involves the preparation of ceramic tapes, screen printing of conductive patterns, lamination, co-firing, and surface finishing. The ability to create high-density, multilayer circuits with embedded components makes LTCC PCBs a powerful solution for advanced electronic applications where performance, miniaturization, and reliability are paramount.
The Application of LTCC PCBs
LTCC (Low-Temperature Co-fired Ceramic) PCBs find applications in a wide range of industries due to their unique combination of electrical, thermal, and mechanical properties. One of the primary areas where LTCC PCBs are widely used is in RF and microwave circuits. The low dielectric constant and loss tangent of the ceramic materials used in LTCC PCBs make them ideal for high-frequency applications, where maintaining signal integrity is critical. As a result, LTCC PCBs are commonly used in communication systems, radar equipment, and satellite technology, where they provide reliable performance in transmitting and receiving high-frequency signals.
Another significant application of LTCC PCBs is in the automotive industry, particularly in advanced driver assistance systems (ADAS), sensors, and power electronics. The ability of LTCC PCBs to withstand harsh environmental conditions, such as high temperatures and vibrations, makes them suitable for use in automotive electronics, where reliability is paramount. For example, LTCC PCBs are used in engine control units (ECUs), airbag systems, and various sensors that monitor and control vehicle performance. Additionally, the excellent thermal management properties of LTCC PCBs make them ideal for power electronics, such as inverters and converters used in electric vehicles (EVs).
The aerospace and defense sectors also benefit from the advantages offered by LTCC PCBs. In these industries, electronic components are often subjected to extreme conditions, including high altitudes, rapid temperature changes, and mechanical shocks. LTCC PCBs, with their robust mechanical properties and thermal stability, are well-suited for such demanding environments. They are used in various aerospace applications, including satellite communications, navigation systems, and avionics, where their reliability and performance are critical. In defense, LTCC PCBs are employed in radar systems, electronic warfare equipment, and missile guidance systems, where precision and durability are essential.
LTCC PCBs are also finding increasing use in medical devices, particularly in implantable and wearable electronics. The biocompatibility and reliability of ceramic materials make LTCC PCBs an excellent choice for medical applications that require long-term stability and minimal interference with biological tissues. For example, LTCC PCBs are used in pacemakers, hearing aids, and diagnostic sensors, where their ability to integrate multiple functions into a compact form factor is highly advantageous. Moreover, the precision manufacturing processes used in LTCC PCB fabrication ensure that the circuits meet the stringent requirements of medical device regulations.
In the field of optoelectronics, LTCC PCBs are used in the packaging and interconnection of optical components, such as lasers, photodiodes, and light-emitting diodes (LEDs). The high thermal conductivity of the ceramic substrate helps to manage the heat generated by these components, ensuring reliable operation and extending their lifespan. Additionally, the
ability to create complex, multilayer circuits within the LTCC substrate allows for the integration of optical components with electronic circuitry, enabling the development of compact and efficient optoelectronic modules.
In summary, LTCC PCBs are used in a diverse range of applications across multiple industries, including RF and microwave communications, automotive electronics, aerospace and defense, medical devices, and optoelectronics. The unique combination of electrical, thermal, and mechanical properties offered by LTCC PCBs makes them an ideal choice for high-performance and reliability-critical applications.
FAQs
What are the main advantages of LTCC PCBs compared to traditional PCBs?
LTCC PCBs offer superior thermal performance, excellent electrical properties, mechanical durability, and the ability to integrate passive components directly into the substrate. These advantages make LTCC PCBs ideal for high-frequency, high-power, and reliability-critical applications, such as in RF and microwave circuits, automotive electronics, and aerospace systems.
How are passive components integrated into LTCC PCBs?
Passive components, such as resistors, capacitors, and inductors, are integrated into LTCC PCBs by embedding them within the ceramic layers during the co-firing process. This is achieved by incorporating resistive or dielectric materials into the conductive paste or using specially formulated layers within the ceramic stack.
What industries commonly use LTCC PCBs?
LTCC PCBs are commonly used in industries such as telecommunications (RF and microwave circuits), automotive electronics (ADAS, sensors, power electronics), aerospace and defense (satellite communications, radar systems), medical devices (implantable and wearable electronics), and optoelectronics (laser and LED packaging).
What are the limitations of LTCC PCBs?
While LTCC PCBs offer numerous advantages, they also have some limitations, such as higher manufacturing costs compared to traditional PCBs, limited material options for certain applications, and potential challenges in achieving very high-density interconnections for complex designs.
Can LTCC PCBs be used in harsh environments?
Yes, LTCC PCBs are well-suited for use in harsh environments due to their excellent mechanical strength, thermal stability, and resistance to thermal expansion. They are commonly used in aerospace, automotive, and defense applications where reliability under extreme conditions is critical.