What is a Hybrid Ceramic PCB?
Hybrid Ceramic PCBs Manufacturer.A Hybrid Ceramic PCB (Printed Circuit Board) manufacturer specializes in producing high-performance circuit boards combining ceramic and traditional materials. These PCBs offer superior thermal conductivity, electrical insulation, and reliability, making them ideal for high-frequency and high-power applications. The manufacturer ensures precision in design and fabrication to meet stringent industry standards, providing solutions for sectors such as aerospace, telecommunications, and automotive. Their advanced technology and expertise support the development of cutting-edge electronics with enhanced durability and performance.
Hybrid Ceramic PCBs are advanced circuit boards that combine the benefits of both ceramic and traditional PCB materials to achieve superior performance in specific applications. These hybrid boards typically use a combination of ceramic substrates for their thermal and electrical properties and organic materials for their flexibility and cost-effectiveness.
Hybrid Ceramic PCBs leverage the strengths of various materials to create a versatile and high-performance circuit board. They often feature a ceramic core or layers that provide excellent thermal conductivity, high electrical insulation, and mechanical robustness. Surrounding this core, traditional PCB materials such as FR4 or flexible polymers are used to offer additional flexibility, ease of fabrication, and cost efficiency.
The Types of Hybrid Ceramic PCBs
Hybrid Ceramic PCBs come in several types, depending on the combination of materials and their intended applications. The main types include:
These boards use a ceramic substrate as the core layer, providing high thermal conductivity and electrical insulation. Surrounding the ceramic core, conventional PCB layers such as FR4 are added to handle the mechanical support and ease of manufacturing. This configuration is beneficial for applications requiring effective heat dissipation and high-frequency performance.
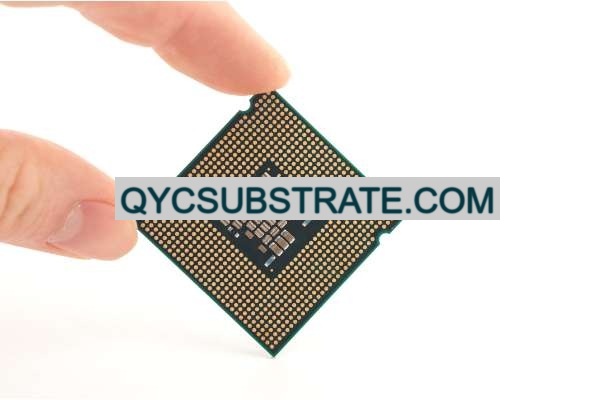
Hybrid Ceramic PCBs Manufacturer
In these designs, a thin ceramic layer is bonded to a flexible organic substrate, such as polyimide. This combination offers the thermal and electrical advantages of ceramic while maintaining the flexibility and conformability of the organic material. Ceramic-on-Flex PCBs are suitable for applications where flexibility and high thermal management are both essential.
These PCBs consist of multiple layers of ceramic and organic materials, stacked and bonded together. This multi-layer approach allows for complex circuit designs and improved thermal management. The layers are arranged to optimize electrical performance, heat dissipation, and mechanical strength, making them suitable for advanced electronic systems.
High-density hybrid PCBs combine ceramic materials with high-density interconnect (HDI) technology to achieve compact and high-performance circuit boards. These PCBs use microvias and fine lines to pack more circuitry into a smaller area while benefiting from the thermal and electrical properties of ceramic materials.
Each type of hybrid ceramic PCB offers distinct advantages based on the combination of materials and the specific requirements of the application.
The Advantages of Hybrid Ceramic PCBs
Hybrid Ceramic PCBs provide several significant advantages by combining the benefits of ceramic and traditional PCB materials:
Hybrid ceramic PCBs offer superior thermal conductivity due to the ceramic components, helping to dissipate heat more effectively than traditional PCBs. This is especially important in high-power applications where managing heat is crucial for reliable operation.
The ceramic materials used in hybrid PCBs provide excellent electrical insulation and low dielectric loss, enhancing signal integrity and reducing electromagnetic interference. This results in improved performance for high-frequency and high-voltage applications.
Hybrid ceramic PCBs benefit from the mechanical strength of ceramic materials, offering better resistance to physical stress, vibration, and shock compared to traditional PCBs. This makes them suitable for use in demanding environments.
By combining ceramic with organic materials, hybrid PCBs can achieve a balance between rigidity and flexibility. This allows for the creation of flexible or conformable circuit boards that maintain high performance and durability.
While ceramic materials can be expensive, hybrid PCBs leverage organic materials to reduce overall costs. This combination allows for cost-effective solutions while still benefiting from the performance advantages of ceramics.
The hybrid approach provides design flexibility, enabling the integration of various materials and technologies to meet specific application requirements. This versatility allows for the development of complex and high-performance circuit boards tailored to diverse needs.
In summary, the advantages of Hybrid Ceramic PCBs include enhanced thermal management, improved electrical performance, mechanical strength, flexibility, cost efficiency, and design versatility. These benefits make hybrid ceramic PCBs a valuable choice for advanced electronic systems and applications.
How to Design a Hybrid Ceramic PCB
Designing a Hybrid Ceramic PCB involves several key steps to ensure optimal performance and manufacturability. The design process begins with defining the requirements and progresses through material selection, layout, and fabrication considerations.
Start by defining the specific requirements of the application, including electrical specifications, thermal management needs, and mechanical constraints. Understanding these requirements will guide the design choices and material selection.
Choose appropriate ceramic and organic materials based on the performance requirements of the PCB. Ceramic materials provide thermal and electrical advantages, while organic materials offer flexibility and cost efficiency. Ensure that the selected materials are compatible and can be effectively integrated.
Develop a detailed circuit schematic that outlines the components and their connections. This schematic serves as the foundation for the PCB layout and ensures that all necessary electrical functions are included in the design.
Using PCB design software, create a detailed layout of the hybrid ceramic PCB. The layout should include the placement of components, routing of conductive traces, and design of thermal management features. Pay attention to minimizing signal paths, reducing parasitic effects, and ensuring proper spacing.
Design the integration of ceramic and organic materials to optimize the performance of the PCB. This may include placing ceramic layers strategically within the PCB structure and incorporating features such as heat sinks or flexible areas.
Incorporate thermal management solutions into the design to address heat dissipation needs. This may include features such as thermal vias, heat spreaders, or integrated cooling mechanisms to ensure effective heat transfer.
Ensure that the design adheres to manufacturing capabilities and constraints. This includes considering factors such as layer alignment, via sizes, and component placement to facilitate efficient fabrication and assembly.
Verify the design’s performance through simulations and testing. This includes checking electrical performance, thermal management efficiency, and mechanical durability. Address any issues identified during this phase before proceeding to manufacturing.
Prepare the design files for fabrication, including detailed specifications for the ceramic and organic materials. Work with a manufacturer experienced in hybrid ceramic PCB production to ensure high-quality results. The fabrication process will involve integrating the materials, applying conductive patterns, and assembling the final PCB.
In conclusion, designing a Hybrid Ceramic PCB involves defining requirements, selecting materials, creating circuit schematics and layouts, integrating materials, incorporating thermal management solutions, and ensuring manufacturability. Proper design practices and verification are essential to achieving a high-performance hybrid ceramic PCB that meets the needs of advanced electronic applications.
Why Use Hybrid Ceramic PCBs Over Other Boards?
Hybrid Ceramic PCBs offer several advantages compared to traditional PCB materials and other types of ceramic PCBs, making them a preferred choice for specific high-performance applications.
Hybrid ceramic PCBs combine the thermal conductivity of ceramic with the cost-effectiveness of organic materials, providing excellent heat dissipation. This is particularly beneficial for high-power and high-density applications where managing heat is critical.
The combination of ceramic and organic materials in hybrid PCBs results in improved electrical performance, including better signal integrity and reduced electromagnetic interference. This makes them suitable for high-frequency and high-voltage applications.
Hybrid ceramic PCBs benefit from the mechanical strength of ceramics, offering better resistance to physical stress and environmental factors compared to traditional PCB materials. This makes them suitable for demanding and rugged environments.
By incorporating organic materials, hybrid ceramic PCBs achieve a balance between rigidity and flexibility while maintaining cost efficiency. This allows for the creation of circuit boards that are both high-performing and economically viable.
The hybrid approach provides design versatility, allowing for the integration of various materials and technologies to meet specific application requirements. This enables the development of complex and customized circuit boards tailored to diverse needs.
Hybrid ceramic PCBs are ideal for applications that require a combination of high thermal conductivity, electrical insulation, and mechanical strength. This includes high-power electronics, RF and microwave devices, and advanced industrial systems.
In summary, Hybrid Ceramic PCBs offer several advantages over traditional and other ceramic PCB materials, including superior thermal management, enhanced electrical performance, mechanical robustness, flexibility, cost efficiency, and design flexibility. These benefits make hybrid ceramic PCBs a valuable choice for high-performance and reliability-critical applications across various industries.
What is the Hybrid Ceramic PCB Fabrication Process?
The fabrication process of Hybrid Ceramic PCBs involves several specialized steps to integrate ceramic and organic materials into a high-performance circuit board. The process begins with material preparation and progresses through various stages to achieve the final PCB.
The process starts with the preparation of ceramic and organic materials. Ceramic powders are mixed with binders to form a paste, while organic materials are prepared for integration with the ceramic components. The materials are carefully controlled to ensure desired properties.
Ceramic layers are shaped using techniques such as pressing, extrusion, or casting. These layers are then dried and sintered at high temperatures to form solid, rigid substrates. Organic materials are prepared for integration with the ceramic layers.
The ceramic and organic layers are integrated based on the design requirements. This may involve bonding ceramic substrates with organic materials using adhesive techniques or lamination processes. The integration must ensure proper alignment and adhesion between the layers.
Once the layers are integrated, conductive patterns are applied using techniques such as screen printing, sputtering, or chemical vapor deposition (CVD). The conductive patterns form the electrical traces, pads, and vias needed for the PCB.
Incorporate thermal management solutions into the design, such as thermal vias or heat spreaders. These features help manage heat dissipation and improve the overall performance of the hybrid ceramic PCB.
The PCB may undergo surface finishing processes to enhance performance and appearance. This includes plating with metals such as gold or silver to improve solderability and protect conductive traces.
The final PCB undergoes rigorous testing and inspection to ensure it meets the required specifications. This includes electrical testing, dimensional inspection, and environmental testing to evaluate performance under various conditions.
The PCB is assembled with components and other necessary elements. This may include mounting electronic components, integrating additional features, and performing final assembly tasks.
In conclusion, the fabrication process of Hybrid Ceramic PCBs involves material preparation, substrate formation, layer integration, patterning, incorporation of thermal management features, surface finishing, testing and inspection, and assembly. Each step is carefully controlled to produce high-performance hybrid ceramic PCBs that leverage the benefits of both ceramic and organic materials.
The Application of Hybrid Ceramic PCBs
Hybrid Ceramic PCBs are used in a variety of applications that benefit from the combination of ceramic and organic materials. Their superior performance characteristics make them suitable for advanced electronic systems and specialized applications.
Hybrid ceramic PCBs are commonly used in high-power electronics where effective heat management and electrical insulation are critical. Applications include power converters, inverters, and motor drives, where the PCB must handle significant power and heat.
The enhanced electrical performance of hybrid ceramic PCBs makes them ideal for RF and microwave applications. These PCBs are used in communication systems, radar equipment, and satellite technology, where high-frequency signal integrity and thermal management are essential.
In the automotive industry, hybrid ceramic PCBs are used in applications such as engine control units (ECUs), advanced driver assistance systems (ADAS), and power electronics. The mechanical robustness and thermal management capabilities of hybrid ceramics make them suitable for automotive environments.
Hybrid ceramic PCBs find use in industrial control systems where durability, reliability, and thermal performance are required. These PCBs are used in control panels, sensors, and industrial automation systems.
In aerospace and defense applications, hybrid ceramic PCBs are employed for their high-performance characteristics. They are used in avionics, communication systems, and other critical applications where reliability and performance are paramount.
The combination of ceramic and organic materials in hybrid PCBs makes them suitable for medical devices requiring high precision and reliability. Applications include diagnostic equipment, implantable devices, and other medical electronics where performance and durability are crucial.
In summary, Hybrid Ceramic PCBs are utilized in various high-performance and specialized applications, including high-power electronics, RF and microwave systems, automotive electronics, industrial control systems, aerospace and defense, and medical devices. Their unique combination of materials provides the performance characteristics needed for advanced electronic systems.
FAQs
What are Hybrid Ceramic PCBs?
Hybrid Ceramic PCBs are advanced circuit boards that combine ceramic and organic materials to achieve superior performance. They leverage the thermal and electrical properties of ceramics and the flexibility and cost efficiency of organic materials.
What types of Hybrid Ceramic PCBs are available?
Common types of Hybrid Ceramic PCBs include ceramic-core hybrid PCBs, ceramic-on-flex PCBs, multi-layer hybrid PCBs, and high-density hybrid PCBs. Each type is designed to meet specific application requirements.
What are the main advantages of Hybrid Ceramic PCBs?
Hybrid Ceramic PCBs offer enhanced thermal management, improved electrical performance, mechanical strength, flexibility, cost efficiency, and design versatility. These advantages make them suitable for high-performance and reliability-critical applications.
How do Hybrid Ceramic PCBs differ from traditional PCBs?
Hybrid Ceramic PCBs combine the benefits of ceramic and organic materials, offering superior thermal conductivity, electrical insulation, and mechanical strength compared to traditional PCBs. They also provide a balance between rigidity and flexibility.
What is the fabrication process for Hybrid Ceramic PCBs?
The fabrication process involves material preparation, substrate formation, layer integration, patterning, incorporating thermal management features, surface finishing, testing, and assembly. Each step is carefully controlled to ensure high performance.