What is Aluminum Nitride (AlN) Ceramic PCBs?
Aluminum Nitride (AlN) Ceramic PCBs Manufacturer.We specialize in manufacturing high-quality Aluminum Nitride (AlN) ceramic PCBs, known for their excellent thermal conductivity and electrical insulation properties. Our advanced production processes ensure precise fabrication and reliability, making our PCBs ideal for high-performance electronic applications, including power electronics and RF circuits. Committed to innovation and quality, we provide tailored solutions to meet the specific needs of our clients.
Aluminum Nitride (AlN) ceramic PCBs are advanced circuit boards made from aluminum nitride, a material known for its exceptional thermal conductivity and electrical insulation properties. AlN ceramics are increasingly used in high-performance electronic applications where managing heat and maintaining electrical isolation are critical.
Aluminum nitride is a compound consisting of aluminum and nitrogen, and it is highly valued for its ability to conduct heat efficiently while providing excellent electrical insulation. These properties make AlN ceramic PCBs particularly suitable for applications involving high power densities and temperature-sensitive electronics.
The fabrication process for AlN ceramic PCBs involves forming a substrate from aluminum nitride powder, which is then sintered at high temperatures to create a dense, solid material. The resulting ceramic substrate is capable of supporting complex circuitry while effectively dissipating heat generated during operation.
The Types of Aluminum Nitride (AlN) Ceramic PCBs
Aluminum Nitride (AlN) ceramic PCBs come in several types, each designed to meet specific application needs and performance requirements. The primary types include single-layer AlN PCBs, multi-layer AlN PCBs, and custom-designed AlN substrates.
Single-layer AlN PCBs are the simplest form, consisting of a single layer of aluminum nitride material. These PCBs are used in applications where a straightforward circuit design is sufficient. Despite their simplicity, single-layer AlN PCBs benefit from the excellent thermal conductivity and electrical insulation provided by aluminum nitride.
Multi-layer AlN PCBs feature multiple layers of aluminum nitride stacked and bonded together. This multilayer structure allows for more complex circuit designs and greater functionality within a compact form factor. Multi-layer AlN PCBs are particularly useful in applications requiring high-density interconnections and effective thermal management. The ability to stack multiple layers also helps in reducing the size of the overall electronic assembly while maintaining high performance.
Custom-designed AlN substrates are tailored to meet specific needs of advanced applications. These substrates can include unique features such as integrated heat sinks, specialized patterns for enhanced thermal performance, or embedded components. Custom designs are often used in cutting-edge technologies where standard AlN PCBs may not meet the required specifications.
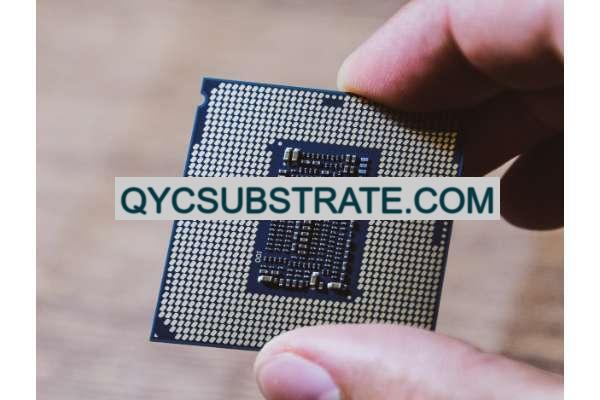
Aluminum Nitride (AlN) Ceramic PCBs Manufacturer
Each type of AlN ceramic PCB offers distinct advantages based on the complexity and requirements of the application. Single-layer boards are cost-effective and suitable for simpler designs, while multi-layer and custom-designed AlN PCBs provide enhanced functionality and performance for more demanding applications.
The Advantages of Aluminum Nitride (AlN) Ceramic PCBs
Aluminum Nitride (AlN) ceramic PCBs offer several significant advantages over traditional PCB materials, making them a preferred choice for high-performance and high-reliability applications.
AlN ceramic PCBs excel in thermal management due to their high thermal conductivity. Aluminum nitride has a thermal conductivity of around 200-250 W/m·K, significantly higher than many other materials used in PCBs. This allows for efficient heat dissipation, which is crucial in high-power electronic devices where excess heat can lead to performance degradation or component failure. By effectively managing heat, AlN PCBs ensure stable operation and enhance the longevity of electronic systems.
AlN ceramics provide excellent electrical insulation, making AlN PCBs suitable for high-voltage applications. The high breakdown voltage and low electrical losses of aluminum nitride ensure reliable performance in circuits with demanding electrical requirements. This makes AlN PCBs ideal for power electronics, RF and microwave devices, and other high-voltage applications.
Aluminum nitride is known for its mechanical strength and durability. AlN ceramic PCBs offer superior resistance to physical stress, vibrations, and shocks compared to traditional PCB materials. This makes AlN PCBs suitable for use in harsh environments such as aerospace, automotive, and industrial applications, where reliability and performance are critical.
AlN ceramics can operate at elevated temperatures without significant degradation in performance. The high temperature tolerance of AlN PCBs makes them suitable for applications involving extreme thermal conditions, such as high-power electronic devices, automotive systems, and aerospace equipment. AlN PCBs maintain their mechanical and electrical properties even under high-temperature conditions.
Aluminum nitride has excellent chemical resistance, making AlN ceramic PCBs suitable for use in corrosive environments. This property is particularly valuable in applications where the PCB may be exposed to harsh chemicals or environments that could otherwise degrade traditional PCB materials.
In summary, the advantages of AlN ceramic PCBs include high thermal conductivity, superior electrical insulation, mechanical strength, high temperature tolerance, and chemical resistance. These benefits make AlN PCBs a valuable choice for advanced electronic systems that require reliable performance under demanding conditions.
How to Design an Aluminum Nitride (AlN) Ceramic PCB
Designing an Aluminum Nitride (AlN) ceramic PCB involves several key steps to ensure optimal performance and manufacturability. The design process begins with defining the electrical and mechanical requirements of the application, followed by the creation of a detailed circuit schematic and layout.
The first step in designing an AlN ceramic PCB is to clearly define the requirements of the application, including electrical specifications, thermal management needs, and mechanical constraints. Understanding the operating conditions and performance requirements will guide the design choices and material selection.
Choose aluminum nitride as the primary substrate material for the PCB. AlN’s high thermal conductivity and electrical insulation properties make it suitable for high-power and high-voltage applications. Additionally, select appropriate conductive materials for the traces and vias that will be used in conjunction with AlN.
Develop a detailed circuit schematic that outlines the components and their connections. This schematic serves as the foundation for the PCB layout and ensures that all necessary electrical functions are included in the design.
Using PCB design software, create a detailed layout of the AlN PCB. The layout should include the placement of components, routing of conductive traces, and design of thermal management features. Pay close attention to minimizing signal paths, reducing parasitic effects, and ensuring proper spacing to avoid interference.
Integrate thermal management solutions into the AlN PCB design to address heat dissipation needs. This may include features such as thermal vias, heat sinks, or specialized patterns to enhance heat transfer away from high-power components.
Ensure that the design adheres to manufacturing capabilities and constraints. This includes considering factors such as layer alignment, via sizes, and component placement to facilitate efficient fabrication and assembly.
Once the design is complete, it is crucial to verify its performance through simulations and testing. This includes checking electrical performance, thermal management efficiency, and mechanical durability. Any issues identified during this phase should be addressed before proceeding to manufacturing.
Prepare the design files for fabrication, including detailed specifications for the AlN substrate and conductive patterns. Work with a manufacturer experienced in AlN PCB production to ensure high-quality results. The fabrication process will involve sintering the AlN substrate, applying conductive patterns, and assembling the final PCB.
In conclusion, designing an Aluminum Nitride (AlN) ceramic PCB involves defining requirements, selecting materials, creating circuit schematics and layouts, integrating thermal management solutions, and ensuring manufacturability. Proper design practices and verification are essential to achieving a high-performance AlN PCB that meets the demanding needs of advanced electronic applications.
Why Use Aluminum Nitride (AlN) Ceramic PCBs Over Other Boards?
Aluminum Nitride (AlN) ceramic PCBs offer several distinct advantages compared to traditional PCB materials, making them an attractive choice for specific high-performance applications.
AlN ceramic PCBs excel in thermal management due to their high thermal conductivity. This property allows for effective heat dissipation, which is essential in high-power applications where heat buildup can lead to performance issues or component failure. Traditional PCB materials, such as FR4, have lower thermal conductivity and may not effectively manage heat in high-power applications.
AlN provides excellent electrical insulation, making AlN ceramic PCBs suitable for high-voltage applications. The high breakdown voltage and low electrical losses of aluminum nitride ensure reliable performance in circuits with demanding electrical requirements. In contrast, traditional PCB materials may have higher electrical losses and lower breakdown voltages, limiting their suitability for high-voltage applications.
Aluminum nitride is known for its hardness and mechanical strength. AlN ceramic PCBs offer superior resistance to physical stress, vibrations, and shocks compared to traditional PCB materials. This makes AlN PCBs ideal for use in harsh environments, such as aerospace and automotive applications, where durability and reliability are critical.
Aluminum nitride can operate at elevated temperatures without significant degradation in performance. AlN ceramic PCBs are capable of withstanding high temperatures, making them suitable for applications involving extreme thermal conditions. Traditional PCB materials, such as FR4, have lower temperature tolerance and may experience performance degradation or failure under high-temperature conditions.
AlN ceramics have excellent resistance to chemical corrosion, making AlN ceramic PCBs suitable for use in environments exposed to harsh chemicals or corrosive substances. This property is beneficial for applications in chemical processing, industrial environments, and other scenarios where traditional PCB materials may be susceptible to chemical damage.
AlN ceramic PCBs allow for the integration of advanced features, such as embedded heat sinks, passive components, and custom designs, to meet specific application needs. This level of integration and customization is often challenging to achieve with traditional PCB materials, which may require additional components or design modifications.
In summary, Aluminum Nitride (AlN) ceramic PCBs offer several advantages over traditional PCB materials,
including high thermal conductivity, superior electrical insulation, mechanical strength, high temperature tolerance, and chemical resistance. These benefits make AlN ceramic PCBs a preferred choice for demanding applications in high-power, high-voltage, and harsh environments.
What is the Aluminum Nitride (AlN) PCB Fabrication Process?
The fabrication process of Aluminum Nitride (AlN) ceramic PCBs involves several specialized steps to produce a high-performance circuit board that leverages the unique properties of aluminum nitride. The process begins with the preparation of AlN substrates and progresses through various stages to achieve the final PCB.
The process starts with the preparation of aluminum nitride powder, which is mixed with binders and additives to form a ceramic paste. This paste is then used to create the AlN substrate. The mixture is carefully controlled to ensure the desired properties of the final PCB, including thermal conductivity, electrical insulation, and mechanical strength.
The AlN paste is shaped into substrates using techniques such as pressing, extrusion, or casting. The substrates are then dried and subjected to a high-temperature sintering process to fuse the aluminum nitride particles together and form a solid, rigid material. The sintering temperature typically ranges from 1600°C to 2000°C, depending on the specific AlN formulation.
Once the AlN substrates are prepared, the next step is to pattern the conductive elements onto the substrate. This is typically done using techniques such as screen printing, sputtering, or chemical vapor deposition (CVD) to apply metal layers, such as copper or silver, onto the AlN surface. The conductive patterns form the electrical traces, pads, and vias needed for the PCB.
If the design involves multiple layers, the patterned AlN substrates are laminated together using high-pressure and high-temperature processes. This step ensures that the layers are firmly bonded and aligned to create a multi-layer PCB. Additional components, such as heat sinks or passive elements, may be integrated during this stage.
The laminated AlN PCB undergoes a co-firing process, where it is heated in a kiln at temperatures exceeding 1600°C. During co-firing, the metal patterns sinter and bond to the AlN substrate, creating a durable and electrically conductive network. The high temperature also ensures that the ceramic substrate achieves its final strength and stability.
After co-firing, the PCB may undergo surface finishing processes to enhance its performance and appearance. This may include plating with gold or other metals to improve solderability and protect the conductive traces. Surface finishes also help to ensure reliable electrical connections and prevent oxidation.
The final step in the fabrication process involves rigorous testing and inspection to ensure that the AlN PCB meets the required specifications. This includes electrical testing to verify connectivity and performance, dimensional inspection to ensure accuracy, and environmental testing to evaluate the PCB’s performance under various conditions.
In conclusion, the fabrication process of Aluminum Nitride (AlN) ceramic PCBs involves material preparation, substrate formation, patterning, lamination, co-firing, surface finishing, and testing. Each step is carefully controlled to produce high-performance AlN PCBs that leverage the unique properties of aluminum nitride for advanced electronic applications.
The Application of Aluminum Nitride (AlN) Ceramic PCBs
Aluminum Nitride (AlN) ceramic PCBs are used in a diverse range of applications due to their exceptional properties, including high thermal conductivity, electrical insulation, and mechanical strength. These properties make AlN PCBs well-suited for applications involving high power densities and temperature-sensitive electronics.
AlN ceramic PCBs are commonly used in power electronics applications, such as power converters, inverters, and motor drives. The high thermal conductivity of AlN helps to manage heat dissipation in high-power devices, ensuring reliable operation and efficiency. AlN PCBs are particularly valuable in applications involving high power densities and rapid switching.
The excellent electrical properties of AlN make it ideal for RF and microwave applications. AlN ceramic PCBs are used in communication systems, radar equipment, and satellite technology, where high-frequency signal integrity is crucial. The low electrical losses and high breakdown voltage of AlN ensure reliable performance in these demanding applications.
AlN ceramic PCBs are employed in aerospace and defense systems due to their durability and high temperature tolerance. Applications include satellite systems, avionics, and missile guidance systems. AlN PCBs can withstand extreme conditions, such as high altitudes, temperature variations, and mechanical stresses, making them suitable for critical aerospace and defense applications.
In the automotive industry, AlN ceramic PCBs are used in advanced driver assistance systems (ADAS), power electronics, and engine control units (ECUs). The ability of AlN PCBs to endure high temperatures and vibrations makes them suitable for automotive environments, where reliability and performance are essential.
AlN ceramic PCBs find use in various industrial applications, including high-temperature sensors, control systems, and industrial power supplies. The chemical resistance and mechanical strength of AlN make it suitable for harsh industrial environments where traditional PCB materials may not perform adequately.
AlN PCBs are used in high-temperature electronic systems, such as geothermal and aerospace applications, where traditional PCBs would fail due to thermal degradation. The high temperature tolerance of AlN ensures that these PCBs maintain their performance and reliability even under extreme conditions.
In summary, Aluminum Nitride (AlN) ceramic PCBs are utilized in diverse applications, including power electronics, RF and microwave devices, aerospace and defense systems, automotive electronics, industrial applications, and high-temperature electronics. The unique properties of AlN make these PCBs a valuable choice for high-performance and reliability-critical applications across various industries.
FAQs
What are the main advantages of Aluminum Nitride (AlN) ceramic PCBs?
Aluminum Nitride (AlN) ceramic PCBs offer high thermal conductivity, superior electrical insulation, mechanical strength, high temperature tolerance, and chemical resistance. These advantages make AlN PCBs ideal for high-power, high-voltage, and harsh environment applications.
How are Aluminum Nitride (AlN) ceramic PCBs different from traditional PCB materials?
AlN ceramic PCBs differ from traditional materials in their high thermal conductivity, superior electrical performance, and mechanical strength. Unlike traditional PCB materials, AlN can operate at higher temperatures and withstand harsher conditions, making it suitable for demanding applications.
What are the typical applications of AlN ceramic PCBs?
AlN ceramic PCBs are used in power electronics, RF and microwave devices, aerospace and defense systems, automotive electronics, industrial applications, and high-temperature electronics. Their unique properties make them suitable for high-performance and reliability-critical applications.
What is the fabrication process for AlN ceramic PCBs?
The fabrication process involves material preparation, substrate formation, patterning of conductive elements, lamination (if multi-layered), co-firing, surface finishing, and rigorous testing. Each step is designed to ensure the high performance and durability of the final AlN PCB.
Can AlN ceramic PCBs be used in high-temperature environments?
Yes, AlN ceramic PCBs are well-suited for high-temperature environments due to their high temperature tolerance and thermal stability. They maintain their performance and reliability even under extreme thermal conditions.