What is Rogers TMM® 10i PCB?
Rogers TMM® 10i PCB Manufacturer.Rogers TMM® 10i PCB Manufacturer specializes in producing high-performance PCBs using Rogers TMM® 10i material. This material is known for its exceptional thermal stability, low dielectric loss, and high mechanical strength, making it ideal for applications in RF and microwave circuits. The manufacturer ensures precise fabrication and quality control, catering to industries that require reliable and efficient PCB solutions for advanced electronic applications.
Rogers TMM® 10i PCB is a high-performance circuit board material designed for microwave and RF applications. Developed by Rogers Corporation, it is specifically engineered to provide high stability and low loss in applications such as communication systems, radar, sensors, and high-frequency electronic devices. The TMM® 10i material offers a unique combination of properties, including low dielectric loss, excellent thermal stability, and mechanical strength, making it ideal for demanding environments.
The dielectric constant (Dk) of Rogers TMM® 10i is 9.8, which makes it exceptionally suitable for high-frequency applications. Its low loss tangent (Df) of approximately 0.002 ensures minimal signal attenuation during high-frequency signal transmission. Additionally, the thermal expansion coefficient (CTE) of TMM® 10i is close to that of copper, which enhances the reliability of the PCB under varying thermal conditions.
Another notable feature of this material is its mechanical robustness and stability. It is easy to handle during manufacturing and can withstand harsh mechanical stresses and environmental conditions in its end-use applications. The TMM® 10i material also exhibits excellent dimensional stability, which is crucial for precise circuit design and fabrication.
The Types of Rogers TMM® 10i PCB
Rogers TMM® 10i PCB can be manufactured in various forms and configurations depending on the application requirements and specific design needs. These types include single-layer, multilayer, and flexible circuit boards, each with its unique advantages and application scenarios.
Single-layer TMM® 10i PCB is primarily used for simple high-frequency circuits such as antennas, filters, and power amplifiers. These circuits typically require low loss and high stability, which are well-suited to the properties of TMM® 10i material.
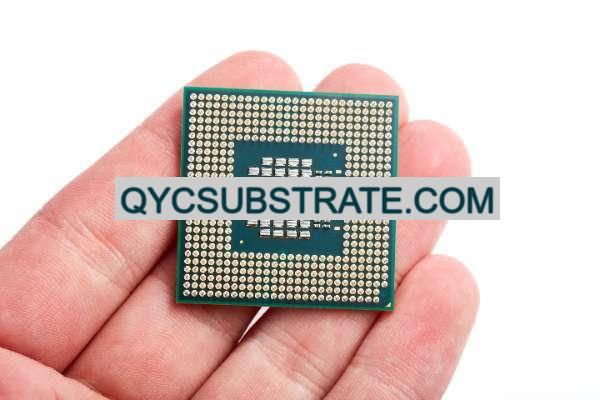
Rogers TMM® 10i PCB Produttore
Multilayer TMM® 10i PCB is used for more complex systems such as communication base stations, radar systems, and high-frequency sensors. These systems need to integrate more functional circuits within limited space, and multilayer construction effectively achieves this. The low loss and high dielectric constant of TMM® 10i material ensure excellent performance in multilayer circuits, maintaining signal transmission stability and reliability.
Flexible TMM® 10i PCB is an emerging application form, mainly used in devices that require flexible installation and complex shapes, such as flexible antennas, wearable devices, and advanced sensor systems. This type of circuit board leverages the mechanical flexibility and high performance of TMM® 10i material, allowing flexible design and installation without compromising electrical performance.
The Advantages of Rogers TMM® 10i PCB
Rogers TMM® 10i PCB offers several significant advantages in high-frequency and microwave applications, making it a widely adopted material in the industry. These advantages include:
The TMM® 10i material has a very low dielectric loss tangent (Df) of approximately 0.002. This means minimal signal attenuation during high-frequency signal transmission, enhancing signal transmission efficiency and quality.
Its dielectric constant (Dk) of 9.8 makes it suitable for use in high-frequency and microwave applications. This characteristic allows TMM® 10i PCB to achieve higher capacitance and more compact designs within a smaller space, ideal for high-density circuits.
The TMM® 10i material’s thermal expansion coefficient (CTE) is close to that of copper, which helps maintain dimensional and performance stability under varying temperature conditions. This is particularly important for circuits exposed to high temperatures or frequent temperature fluctuations.
TMM® 10i material possesses excellent mechanical properties, allowing it to withstand high stresses and harsh working environments. This ensures high reliability and durability during both manufacturing and use.
TMM® 10i material is easy to process and handle, suitable for various manufacturing processes, including drilling, plating, and etching. This simplifies the manufacturing process, reduces production costs, and improves production efficiency.
How to Design a Rogers TMM® 10i PCB?
Designing a Rogers TMM® 10i PCB requires careful consideration of material properties, application requirements, and manufacturing processes. Here are some key steps and points to keep in mind during the design process:
First, choose the appropriate TMM® 10i material thickness and dielectric constant based on the application requirements. This step is crucial as the material selection directly affects the circuit’s performance and stability.
When laying out the circuit, consider the high-frequency signal transmission paths and grounding design. Minimize signal path lengths to avoid signal interference and reflection. Additionally, design a good grounding plane and power distribution network to ensure circuit stability and signal integrity.
Impedance control is essential in high-frequency circuit design. When using TMM® 10i material, accurately calculate and control the impedance of transmission lines to ensure signal integrity and transmission efficiency. This typically involves using electromagnetic simulation software for modeling and verification.
Although TMM® 10i material has excellent thermal stability, thermal management should still be considered during design. Particularly for high-power applications, design effective heat dissipation channels and heatsinks to prevent overheating from affecting circuit performance.
During the design process, consider the processing characteristics of TMM® 10i material. For example, parameters for drilling and etching should be confirmed with the manufacturer to ensure smooth manufacturing and high product quality.
Why Use Rogers TMM® 10i PCB Over Other Boards?
Choosing Rogers TMM® 10i PCB over other types of PCB materials offers multiple benefits, making it stand out in specific applications:
The low dielectric loss and high dielectric constant of TMM® 10i material make it excellent for high-frequency and microwave applications. Compared to traditional FR-4 materials, TMM® 10i maintains lower signal attenuation and better signal integrity at higher frequencies.
The thermal expansion coefficient of TMM® 10i material is close to that of copper, allowing it to maintain dimensional stability in high-temperature environments and reduce thermal stress-induced circuit failures. Its superior mechanical strength ensures reliable performance in harsh working conditions.
TMM® 10i material is easy to process and handle, suitable for various complex manufacturing processes. This allows designers to achieve more complex and higher-density circuit designs while ensuring manufacturability and cost-effectiveness.
Due to its unique performance advantages, TMM® 10i PCB is widely used in communication, aerospace, military, radar, and high-frequency sensor fields. Compared to other materials, TMM® 10i better meets the high performance and reliability requirements of these fields.
What is the Rogers TMM® 10i PCB Fabrication Process?
The fabrication process of Rogers TMM® 10i PCB involves several key steps, each requiring precise control to ensure the final product’s quality and performance. Here are the main fabrication steps:
Choose the appropriate TMM® 10i material and prepare it according to design requirements. The material’s thickness and dielectric constant need to be selected based on the circuit design.
Drill holes in the TMM® 10i material according to the design drawings. This step requires precise control of hole location and diameter to ensure consistency with the circuit layout.
Plate the drilled holes and circuit paths to form conductive layers, usually using copper. This step requires ensuring uniform plating thickness and good conductivity.
Use photolithography to transfer the circuit pattern onto the TMM® 10i material. Photographic materials and masks are used to expose the circuit pattern onto the material surface.
Use chemical etching to remove unwanted conductive layers, leaving only the designed circuit paths. This step requires precise control of etching time and solution concentration to ensure pattern accuracy.
For multilayer TMM® 10i PCBs, laminate and bond the circuit layers together. This step requires a high-temperature and high-pressure environment to ensure good bonding and electrical connection between layers.
Apply surface treatments such as gold plating, tin plating, or other protective layers to the circuit board as needed. This enhances the board’s durability and conductivity.
Finally, perform electrical performance testing and visual inspection on the fabricated TMM® 10i PCB to ensure it meets design requirements and quality standards.
The Application of Rogers TMM® 10i PCB
Rogers TMM® 10i PCB is widely used in various high-frequency and microwave applications due to its excellent performance. Here are some of the main application areas:
TMM® 10i PCB is extensively used in wireless communication base stations, satellite communications, and mobile communication devices. These systems require efficient high-frequency signal transmission with low loss, which TMM® 10i material provides.
Due to its high dielectric constant and low loss characteristics, TMM® 10i PCB is commonly used in military and civilian radar systems. These systems operate at high frequencies, and TMM® 10i’s stable performance and reliability make it an ideal choice.
High-frequency sensors used in various industrial and scientific applications require precise signal transmission and processing. TMM® 10i PCB plays a crucial role in these sensors, ensuring data accuracy and reliability.
TMM® 10i PCB is widely used in the aerospace sector, including satellite systems, navigation devices, and flight control systems. Its excellent thermal stability and mechanical strength allow it to perform reliably in extreme environments.
In certain high-precision medical devices such as MRI scanners and high-frequency ultrasound equipment, TMM® 10i PCB ensures efficient signal transmission and device reliability.
FAQs
What are the main advantages of Rogers TMM® 10i PCB?
The main advantages include low dielectric loss, high dielectric constant, excellent thermal stability, mechanical strength, and ease of processing.
What application areas is TMM® 10i PCB suitable for?
TMM® 10i PCB is suitable for communication systems, radar systems, high-frequency sensors, aerospace, and medical devices, among other high-frequency and microwave applications.
What is the difference between TMM® 10i PCB and traditional FR-4 PCB?
TMM® 10i PCB offers lower signal loss and higher dielectric constant at high frequencies compared to traditional FR-4 PCB, which is typically used at lower frequencies and has less stable performance.
What factors should be considered when designing a TMM® 10i PCB?
Factors to consider include material selection, circuit layout, impedance control, thermal management, and manufacturing processes to ensure the final product’s performance and reliability.