What is Rogers 4400 PCB?
RO4000 dielectric materials have long been used in combination with FR-4 cores and prepreg as a means to achieve a performance upgrade of standard FR-4 multi-layer designs. RO4003C™, RO4350B™ and RO4000 LoPro® glass reinforced hydrocarbon/ceramic laminates have been used in layers where RF / microwave frequency, dielectric constant (Dk), or high-speed signal requirements dictate high performance materials. FR-4 cores and prepreg are still commonly used to inexpensively form less critical signal layers.
Features
- Prepreg grades based on RO4000 series core materials
- Low z-axis coefficient of thermal expansion ranging from 43 to 60 ppm/°C
- Sequential lamination capable
- Lead free solder processing compatible
Benefits
- Compatible in multi-layer board constructions with RO4003C, RO4350B, RO4835™, RO4360G2™ or RO4000 LoPro laminates.
- CAF resistant
- High frequency thermoset prepreg compatible with FR-4 bond temperatures
- High reliability plated through-hole
Rogers 4400 PCB Produttore,”Rogers 4400 PCB Produttore” refers to a company specializing in the production of PCBs using Rogers 4400 series materials. These materials are known for their high-frequency performance and reliability in electronic applications requiring stringent signal integrity and thermal management.
Rogers 4400 PCB is a high-performance printed circuit board (PCB) utilizing Rogers Corporation’s 4400 series of specific materials. This material is known for its excellent electrical and thermal properties, making it particularly suitable for demanding high-frequency and high-speed applications. Designed and manufactured to meet the precise signal transmission and stable performance requirements of modern electronic equipment, Rogers 4400 boards are widely used in wireless communications, RF circuits and microwave applications.
Rogers 4400 PCB material has extremely low dielectric loss, which means energy loss during signal transmission is minimized, keeping signals clear and stable. Its stable dielectric constant ensures the consistency and reliability of the circuit, especially when operating at high frequencies, which can effectively reduce signal distortion and cross-interference. These features make the Rogers 4400 PCB ideal for wireless communications and RF front-end equipment, capable of supporting complex data processing and transmission requirements.
In addition to its excellent electrical characteristics, Rogers 4400 PCB also exhibits excellent thermal management capabilities. Its material has good thermal conductivity and thermal stability, and can effectively disperse and handle the heat generated in the circuit. This is critical for high power density applications and long-duration equipment, ensuring circuit stability and long-term reliability. Therefore, Rogers 4400 PCB is widely preferred in electronic equipment requiring high performance and reliability.
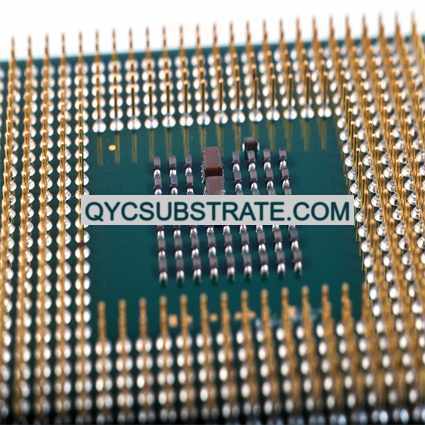
Rogers 4400 PCB Produttore
Rogers 4400 PCBs are used in a variety of high-frequency and high-speed electronic equipment, including but not limited to communications infrastructure, satellite communications, radar systems, medical equipment, and aerospace technology. For example, in the development of 5G communication technology, Rogers 4400 PCB can support large-capacity data transmission and complex radio frequency signal processing, providing key support for network performance improvement and data security.
In summary, Rogers 4400 PCB is an advanced printed circuit board material that combines excellent electrical performance with superior thermal management capabilities. Its low dielectric loss, stable dielectric constant and good dimensional stability make it the first choice for modern high-frequency electronic designs. As communications technology and radio frequency applications continue to evolve, Rogers 4400 PCB will continue to play a key role in new generations of electronic devices, driving technological progress and market innovation.
The types of Rogers 4400 PCB
Rogers 4400 PCB is a high-performance printed circuit board (PCB) utilizing Rogers Corporation’s 4400 series of specific materials. This material combines excellent electrical and thermal properties, making it excellent in high-frequency and high-speed applications. Rogers 4400 PCB can be designed as a single-layer, double-layer or multi-layer board according to specific application requirements, each type has its specific advantages and applicable scenarios.
Single-layer Rogers 4400 PCBs are suitable for simple circuit designs and cost-sensitive applications. It is typically used in low-complexity electronics such as consumer electronics, sensors, and basic control systems. Single-layer PCBs are cheaper to manufacture and have a simple design, making them particularly suitable for projects that require high-volume production and cost control.
The double-layer Rogers 4400 PCB adds a layer of copper foil to a single-layer board, allowing the board to accommodate more complex circuit designs. This type of PCB is suitable for applications requiring higher integration and more complex layouts. In fields such as communication infrastructure, industrial control, and automotive electronics, double-layer PCB can support the integration of multiple functional modules and improve the performance and reliability of the overall system.
Multilayer Rogers 4400 PCBs are the most complex type of design, typically containing four or more layers of circuit stacking. This design provides higher circuit density and better signal integrity, suitable for applications requiring a high degree of integration and high-frequency transmission. In satellite communications, medical equipment, and advanced consumer electronics, multilayer PCBs can support complex signal processing, data transmission, and power management while maintaining circuit stability and reliability.
In the field of communication infrastructure, the multi-layer design of Rogers 4400 PCB can support complex signal processing and multi-channel data transmission, ensuring efficient data transmission and system stability.
Satellite communications systems require PCBs to maintain a high degree of stability and long-term reliability in extreme environments, and multi-layer Rogers 4400 PCBs meet these requirements and support complex signal processing and data transmission tasks.
In medical devices, Rogers 4400 PCB’s multi-layer design can integrate various sensors and control units, supporting sophisticated data processing and fast-response functions to improve device performance and safety.
Rogers 4400 PCBs offer single-layer, dual-layer and multi-layer design options, each type offering unique advantages and applicability. From low-cost simple circuits to highly complex multi-functional applications, Rogers 4400 PCB can meet the needs of different industries and application fields, providing strong support and flexibility for the design and manufacturing of electronic products.
The advantages of Rogers 4400 PCB
Rogers 4400 PCB is a high-performance printed circuit board (PCB) developed by Rogers Corporation and widely used in high-frequency and high-speed electronic equipment. Its material properties enable it to demonstrate superior performance advantages in a number of key areas.
Rogers 4400 PCB material has excellent high frequency properties and can effectively support frequency ranges from hundreds of megahertz to several gigahertz. This makes it excellent in high-frequency environments such as 5G communications, radio frequency (RF) front-end and microwave applications. Compared with traditional FR-4 boards, Rogers 4400 PCB significantly reduces losses in signal transmission, ensuring signal accuracy and stability.
Rogers 4400 PCB excels in high-speed data transmission and precision signal processing due to its low dielectric loss properties. This excellent signal integrity means that in complex circuit layouts and highly integrated applications, Rogers 4400 PCB can reduce signal attenuation and distortion, ensuring high-fidelity transmission of data.
Rogers 4400 material has good thermal conductivity and thermal stability to effectively manage heat in circuits. In applications with high power density and long operation times, stable thermal management is critical to circuit reliability and longevity. Rogers 4400 PCB effectively disperses and releases heat to maintain a stable operating temperature of the circuit, thereby extending the life of the device and performance stability.
In addition to its excellent electrical and thermal properties, Rogers 4400 PCB offers excellent mechanical stability. This allows it to maintain the shape and size of the sheet under complex environmental conditions and is less susceptible to external environmental influences or mechanical stress. So whether in aerospace, military applications or medical equipment, Rogers 4400 PCBs maintain their performance and reliability.
Designing and manufacturing Rogers 4400 PCBs requires strict process control and a high level of technical support. Rogers Corporation provides professional design guidance and manufacturing advice to ensure that every PCB meets the highest quality standards and performance requirements. From material selection to final production process, the Rogers 4400 PCB manufacturing process is carefully designed and rigorously monitored to ensure customers receive a consistently high-quality product.
In summary, Rogers 4400 PCB has become the first choice in the design of many high-demand electronic equipment due to its excellent high-frequency characteristics, low loss, stable thermal performance and high mechanical stability. Its wide range of applications in communications, radio frequency, microwave and medical fields fully demonstrate its excellent performance and reliability in various complex applications.
How to Design a Rogers 4400 PCB?
Designing a Rogers 4400 PCB is a complex and critical engineering process that requires a deep understanding of the impact of material properties and circuit layout on performance. The following are the key considerations and steps for designing a Rogers 4400 PCB:
First, engineers must fully understand the electrical and thermal properties of the Rogers 4400 material. Rogers 4400 PCB material has low dielectric loss and stable dielectric constant, making it suitable for high frequency and high speed applications. During the design process, it is critical to understand the impact of these characteristics on signal transmission and overall circuit performance.
Secondly, using professional CAD (computer-aided design) software for circuit layout design is a crucial step. Engineers need to accurately plan component placement and wire paths on the circuit board to ensure that the signal transmission path is as short as possible to reduce signal delay and loss. In addition, avoiding unnecessary interaction interference (such as crosstalk) is also an important consideration in the design.
In high-frequency applications, electromagnetic compatibility (EMC) principles are crucial. Designers need to take measures such as good ground wire design, shielding techniques and good layout planning to reduce electromagnetic radiation and suppress electromagnetic interference. These measures can not only improve the stability and reliability of the circuit, but also ensure the normal operation of the PCB in a complex electromagnetic environment.
Ultimately, selecting the appropriate manufacturing process is critical to ensuring accuracy and reliability in PCB manufacturing. Surface mount technology (SMT) and multi-layer stacking technology are commonly used processes in modern PCB manufacturing, enabling higher component integration and more complex circuit designs. Every step in the manufacturing process, including material pre-processing, lamination processes, drilling and electroless copper plating, must be tightly controlled to ensure the final PCB meets design specifications and performance requirements.
To sum up, designing a Rogers 4400 PCB requires comprehensive consideration of multiple factors such as material properties, circuit layout, electromagnetic compatibility, and manufacturing processes. Through systematic design and strict process control, the excellent performance and reliability of PCB in high-frequency and high-speed applications can be ensured.
Why use ceramic Rogers 4400 PCB over other boards?
In specific application scenarios of high-temperature environments and high-frequency signal transmission, choosing ceramic PCBs (such as alumina ceramics) has obvious advantages over traditional fiberglass-reinforced boards (such as FR-4 boards). Here is a detailed explanation and comparison:
Ceramic PCB materials typically have higher thermal conductivities than traditional materials, which means they are more efficient at dispersing and managing the heat generated in circuits. Thermal management is critical in high-power-density applications such as radar systems, high-power amplifiers, or other devices that require long periods of operation. Ceramic PCBs can help keep circuit components operating at stable temperatures, extending the life and reliability of your equipment.
Ceramic PCBs offer better mechanical stability than common FR-4 boards. Their structure is stronger and more durable, resistant to temperature changes and physical shock, and less prone to expansion or contraction. This stability is particularly important for applications that require high precision and long-term stability, such as those in aerospace, defense and medical equipment.
Ceramic PCBs have a low dielectric constant, which is one of their key advantages in high-frequency circuit design. A low dielectric constant means less signal loss during transmission and reduces signal distortion. In the radio frequency (RF) and microwave bands, signal integrity is critical to the accuracy and reliability of data transmission. The ability of ceramic PCBs can effectively reduce interference and loss during signal transmission, thereby improving system performance and stability.
Ceramic PCBs are widely used in demanding RF and microwave circuit designs such as antenna systems, satellite communications, radar technology and medical imaging equipment. These applications often require highly stable electrical performance and reliability to meet long-term operation requirements in complex environments. Ceramic PCBs not only maintain stable performance in high temperatures and harsh environments, but also provide highly integrated solutions in compact spaces.
In summary, the choice of ceramic PCBs over traditional FR-4 boards is based on their superior thermal management capabilities in high-temperature environments, excellent mechanical stability, and low dielectric constant. These characteristics make ceramic PCB an indispensable key component in high-frequency and high-performance electronic equipment, providing important support and guarantee for the development of modern technology.
What is the Rogers 4400 PCB Fabrication Process?
Manufacturing Rogers 4400 PCBs is a complex and delicate process involving multiple critical steps, each of which has a significant impact on the quality and performance of the final product. The following is a detailed description of the manufacturing process:
The process of manufacturing a Rogers 4400 PCB includes multiple process steps including material selection, pre-processing, lamination, drilling, electroless copper plating, patterning, metallization and surface treatment. The specific content and importance of each step will be introduced step by step below:
The first step in manufacturing a high-performance PCB is choosing the right materials. For Rogers 4400 PCBs, it is critical to select high-performance 4400 series-specific materials from Rogers Corporation. After material selection, pre-treatment is required to ensure that the surface of the board is smooth, clean, and free of any dirt or oxides. This is the basis for ensuring the smooth progress of subsequent process steps.
Next is the lamination process of the PCB. Lamination is a critical step in stacking layers of pre-processed materials together to form a multi-layer structure. Each layer contains a specific circuit design, and the dielectric between the layers is tightly bonded to the copper foil through thermal pressure. This process ensures the overall structural stability and mechanical strength of the circuit board, as well as the consistency and reliability of signal transmission.
After lamination is completed, precise drilling operations are required. These holes are used for connections between different layers on the circuit board and for pin penetrations when mounting components. The drilling process must be very precise, because the accuracy of the hole location directly affects the quality and reliability of subsequent circuit connections.
After drilling is completed, electroless copper plating is performed. This step is to establish a conductive path in the drilled hole to ensure the continuity of the circuit. Patterning is then performed, using photolithography and chemical etching to transfer the designed circuit pattern to the surface of the copper foil. This process precisely controls the formation of the circuit, ensuring the precise location and size of each line and pad.
Finally, metallization and surface treatment are performed. Metallization is the application of a layer of protective metal, usually tin or gold plating, to the surface of a circuit board to protect the copper conductors from oxidation or corrosion. Surface preparation includes smoothing, cleaning and the application of anti-corrosion coatings to ensure joint reliability and long-term stability.
Quality control and testing are crucial aspects of the entire manufacturing process. Through strict parameter control and multiple inspection methods (such as X-ray inspection, electrical testing and optical inspection), it is ensured that each Rogers 4400 PCB meets the design requirements and standards. These measures not only ensure product consistency and stability, but also ensure the reliability and durability of high-performance PCBs during use.
In summary, the manufacturing process of Rogers 4400 PCB requires highly professional technology and sophisticated equipment to meet the strict requirements of modern electronic equipment for high frequency, high speed and stable performance. Carefully designed and precisely controlled processes enable the production of PCBs that meet high standards, supporting the development and innovation of electronic devices in a variety of key application areas.
The application of ceramic Rogers 4400 PCB
The Rogers 4400 PCB is an advanced printed circuit board (PCB) designed for high frequency and high speed applications and is found in a wide range of applications in modern electronics. Its excellent electrical performance and stability make it the first choice in various key fields. The following is a detailed introduction to its main application areas:
Communications infrastructure is one of the important application areas for Rogers 4400 PCBs. With the rapid development of mobile communication networks, especially the promotion of 5G technology, there is an increasing demand for high-frequency and high-speed data transmission. The low dielectric loss and stable dielectric constant of Rogers 4400 PCB ensures minimal loss during signal transmission and the highest data transfer rate. It is widely used in key components such as base station antennas, radio frequency front-end modules, and microwave transmission equipment, providing a solid foundation for the efficient operation of modern communication networks.
In the field of satellite communications, the reliability and stability of the Rogers 4400 PCB is particularly important. Satellite communication systems require electronic equipment and components that can operate stably for long periods of time under extreme environmental conditions. The material properties of Rogers 4400 PCB enable it to maintain excellent performance in high vacuum, high radiation and a wide temperature range, ensuring stable transmission of satellite signals and data processing. It is used in satellite payloads, transmitting and receiving modules of communication satellites, and satellite ground control equipment, providing reliable support for global communications.
Radar systems have important applications in both military and civilian fields and require high sensitivity and precise signal processing capabilities. Rogers 4400 PCB can meet the strict requirements of radar systems for high-frequency and microwave signal processing, supporting rapid transmission and accurate detection of radar signals. It is widely used in key components such as radar antenna arrays, signal processing units, waveform generators and receiver modules, improving the performance and reliability of radar systems in complex environments.
In the medical device field, particularly in medical imaging and wireless medical devices, the low loss and high frequency characteristics of Rogers 4400 PCB are very important. Medical devices need to be able to efficiently transmit and process medical data and ensure data accuracy and security. Rogers 4400 PCB is used in key electronic components of high-tech medical equipment such as MRI equipment, ultrasound imaging systems, pacemakers and wireless monitoring equipment, providing reliable technical support for medical diagnosis and treatment.
In the aerospace field, electronic equipment is required to operate stably in extreme space environments, and lightweight design is particularly important. Rogers 4400 PCB not only has excellent high-frequency characteristics and thermal management capabilities, but also can withstand high vibration and shock, making it suitable for complex electronic systems in aerospace devices. It is widely used in spacecraft communications, navigation control, data acquisition and satellite navigation systems, contributing important electronic solutions to the advancement of aerospace technology.
In summary, Rogers 4400 PCB has become an indispensable and important component in high-frequency and high-speed electronic equipment due to its excellent performance characteristics and wide range of applications. Whether in the fields of communications, satellites, radar, medical or aerospace, it plays a key role in promoting the development and application of modern technology.
FAQs
What frequency ranges are Rogers 4400 PCB suitable for?
Rogers 4400 PCBs are designed primarily for use over a wide range of high frequencies, typically covering frequency ranges from a few hundred megahertz to several gigahertz. This makes it particularly suitable for 5G communications, radio frequency front-end equipment, microwave communication systems and other application scenarios that require high-frequency transmission and precise signal processing. Rogers 4400 PCB has excellent electrical properties and a stable dielectric constant to ensure excellent performance in high-speed data transmission environments.
How is the thermal management of the Rogers 4400 PCB?
Rogers 4400 PCB material has excellent thermal conductivity and thermal stability to effectively manage heat in circuits. This makes it ideal for applications requiring high power density and long operation times. In high-frequency and high-speed circuits, good thermal management capabilities are critical to maintaining signal stability and extending circuit life.
Why choose Rogers 4400 material over other high frequency materials?
Rogers 4400 material combines excellent electrical properties with robust mechanical properties and chemical stability. It has lower dielectric loss and better signal integrity than traditional FR-4 boards, making it suitable for demanding RF and microwave circuit designs. In addition, Rogers 4400 PCB material has long been proven in a wide range of industrial and commercial applications, ensuring its reliability and stability.